
What Are the Differences Between AAC and ICF Construction?

Insulated concrete form (ICF) and autoclaved aerated concrete (AAC) wall systems are a modern alternative to traditional wood or concrete masonry units (CMU). ICF and AAC both claim to provide builders a more straightforward, quicker, and more flexible construction method than conventional methods, saving time and money. In addition, both ICF and AAC wall systems offer eco-friendly, fire-resistant, and sound-controlled construction.
However, ICFs, like Fox Blocks, provide several advantages over AAC. Specifically, ICF provides significantly more energy efficiency, disaster resistance, and durability, along with indoor air quality (IAQ), than AAC.
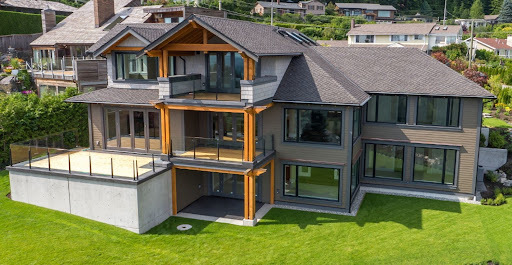
What is Autoclaved Aerated Concrete?
Factory-produced, cement-masonry precast autoclaved aerated concrete (AAC) combines sand, cement, lime, water, and an expansion agent (like aluminum powder) to form 8-inch blocks, panels, or specialty shapes, all molded and cut precisely into dimensional units. In addition, AAC contains millions of tiny air cells (80 percent of its total composition), giving it an insulation value of R-8 — better than brick, concrete, or other masonry products.
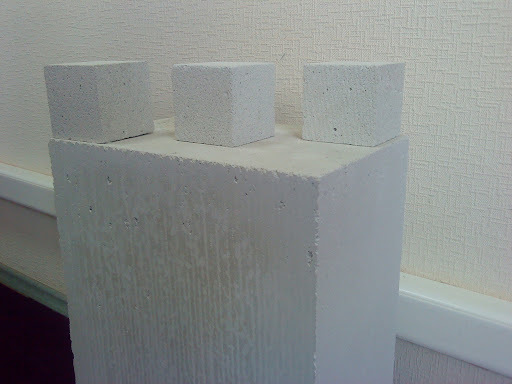
Cost of AAC Blocks
As of 2018, a basic 8 x 8 x 24 inch block of AAC costs about $2.20 to $2.50/ft2; 10 to 25 percent more than standard concrete blocks. However, the lightweight nature of AAC makes it easier to handle and install, lowering labor costs over CMU.
Shapes and Sizes of AAC
AAC units come as panels, blocks, and specialty shapes. Blocks stack similar to CMUs, while panels install vertically, spanning the full height of the building.
Panels extend from floor to ceiling up to 20 feet, with a width of 24 inches and thicknesses of 6, 8, 10, and 12 inches (4 inches thick for interiors). Typically, workers place the vertical cells at the corners, on either side of openings, with 6- to 8-foot spacings along a wall. However, because of the panel’s heavy weight, you will need a crane to place them.
8-inch high and 24-inch long blocks come in 4, 6, 8, 10, and 12-inch thicknesses, weighing about 33 pounds. Workers lay the first course of AAC blocks in a traditional mud bed, leveling when finished. They lay subsequent courses on an application thin-set mortar with a notched trowel. Fortunately, the precision-cut blocks make it easy to keep a wall square and plumb during installation.
AAC offers several specialty shapes:
Lintel blocks or U-shaped bond beams in 8-, 10-, and 12-inch thicknesses
Groove-and-tongue block that connects to adjacent units without mortar at vertical edges
Cored blocks create vertical reinforced grout cells
The Pros of Autoclaved Aerated Concrete
AAC walls offer several advantages to builders: installation ease, environmentally-friendly, fire-resistant, and energy-efficient.
Ease of Installation of AAC
Lightweight AAC units combine insulation and structural capabilities, offering masons a quick and easy way to install a wall compared to heavy concrete masonry blocks, saving time, money and lessening job site injury.
Moreover, the lightweight/cellular properties of AAC make it easy to cut, shape, and shave, accept screws and nails, and route to create chases for electrical conduits and smaller-diameter plumbing runs. These features give AAC design and construction flexibility, making it easy to adjust in the field.
Cutting and shaping AAC with simple hand and power tools reduces noise and dust-related health risks, compared to the high-speed diamond saws used to cut CMUs.
Eco-Friendly AAC
Made from natural products, recyclable AACs provide reasonable insulation value. However, its production uses a lot of energy, but 50 percent less than concrete products.
Fire-Resistance AAC
Non-combustible, eight-inch thick AAC achieves a four-hour rating; and will not burn or give off toxic fumes.
High Sound Reduction for AAC Walls
The lightweight nature of AAC contributes towards a high sound reduction both from outdoor noises and between rooms.
The Cons of Autoclave Aerated Concrete
Before choosing an AAC wall system, a homeowner should consider these problems: limited availability, lower strength and insulation value, and water absorption.
The limited availability of AAC may make it challenging to find, although manufacturers will ship the product.
When fully bedded, AAC creates walls with monolithic strength and performances. However, compared to most concrete products or systems, AAC's lower strength requires reinforcing the AAC blocks or panels in load-bearing applications.
AAC only provides a minimal R-value and will require the application of additional continuous insulation to meet energy code requirements.
Water absorbing and crumbly AAC requires a plaster-type finish or another protective veneer on its surface, like stucco and heavy-bodied coatis, ceramic tile, and full-or thin-brick veneers to prevent deterioration if left exposed to outdoor elements.
What is ICF Construction?
Builders use ICFs, like Fox Blocks, for above- and below-grade wall systems for everything from single- and multi-family residential, schools, warehouses, office buildings, hospitals, movie theaters, and more. ICFs produce high-performing, durable, and energy-efficient buildings (R-22 CI), meeting if not surpassing ASHRAE 90.1 and 2021 IECC requirements. In addition, quick and easy ICF construction provides a safe work environment, saving time and money and limiting the risk of injury.
The Cost of ICF Construction
ICF's, inherently, offer more to the wall assembly with continuous insulation, air barrier and vapor retardant. These added benefits make the unit cost per sq.ft. more than an AAC unit. Thankfully, labor costs to install ICFs is cheaper than skill masonry costs for AAC installations and ICFs provide long-term financial benefits, offsetting initial construction costs.
The Shapes of ICFs
Many manufacturers offer insulation concrete forms (ICFs) in block and panel forms:
ICF block systems consist of hollow, open-ended panels (often made of either extruded polystyrene foam or expanded polystyrene) separated by six to eight inches of reinforced rebar. Before pouring the concrete, the interlocking units are dry-stacked, similar to building with Lego bricks. After the concrete cures, the inner and outer polystyrene ICF panels create a permanent exterior framework. These panels permit the installation of plumbing and electrical conduits later in the building process.
ICF panel systems, often applied to tilt-up construction, involve pouring the walls horizontally on the structure’s floor slab at the job site. A crane lifts the panels into place, where steel braces temporarily secure the panels until workers can weld permanent fasteners into the panel’s joints, roofline, and footings.
6 Benefits of ICF Construction
Strong, flexible, and easy to install ICF construction creates modern structures that offer energy efficiency, durability, disaster resistance, and good IEQ. For these reasons, many of today’s architects, contractors, and building and home owners are choosing ICF construction over other wall construction methods.
A recent report expects the North America ICF market to grow by more than 5 percent between 2016 to 2026, driven by the need for energy-efficient and disaster-resistant buildings, along with the increasing demand for high-rise construction and reduced building times.
1. Quick and Simple Installation
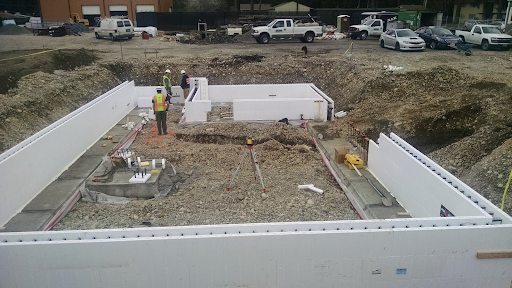
ICFs, like Fox Blocks, provide builders with a fast and straightforward method for constructing above- and below-grade walls, saving time and money.
Fox Blocks walls combine five-building steps: structure, air barrier, structure, vapor retarder, continuous insulation, and attachment. The all-in-one wall system lessens the need to manage multiple trades, significantly hastening delivery time while achieving the project goals.
In addition, the strength and flexibility of ICF construction can accommodate most building sizes, styles, and plans. The ease in cutting and shaping ICFs allows for customized designs, such as large openings, cathedral ceilings, curved walls, long ceiling spans, and custom angles.
2. Eco-Friendly ICFs
Eco-friendly ICFs, like Fox Blocks ICFs, lack volatile organic compounds (VOC), which can compromise the IAQ of the structure. Also, Fox Blocks contribute to a structure’s sustainability because they contain a minimum of 40 percent recycled content by weight.
3. Disaster-Resistant ICF Construction
The strength and resistance of ICFs provide several significant disaster-resistant components, reducing the costs and hassles of repairing or even rebuilding.
ICFs, like Fox Blocks, provide passive fire protection, which limits the spread of flames during a fire. ICF walls do not burn, bend, or soften like steel.
ICF wall systems, with steel-reinforced concrete, contribute towards a continuous load path. During a severe wind event, the path holds the walls, roof, floors, and foundation together by moving the force from the roof, walls, and other building components toward the foundation and finally into the ground.
ICF walls also provide airborne debris from penetrating the wall system during severe wind events.
The sheer walls of ICF structures extend the entire height and all sides of the building, making them earthquake resistant. During an earthquake, ICF walls effectively resist intense sideways (lateral) in-plane forces that push the top of the wall one way, while the bottom stays stationary or is pushed in the opposite direction (racking the wall).
4. ICFs Contribute Towards Excellent IEQ
ICF structures create healthy and comfortable structures, and can improve the well-being and productivity of the occupants.
Moisture-resistant ICF walls minimize, if not prevent, the growth of unhealthy mold.
ICF wall systems limit the transfer of sound from the outside to the inside of a structure.
5. Energy-Efficient ICF Construction
The thermal mass and high R-values of ICFs contribute to tight thermal building envelopes, creating comfortable buildings and homes with lower utility costs.
6. Durable ICF Construction
ICF’s create solid continuous monolithic concrete walls (perm rating of 1.0), and manage moisture accumulation in the wall system, preventing the growth of unhealthy and structurally damaging mold and rot.
The Downside of ICF Construction
An ICF structure looks just like an AAC structure, however, ICFs produce wider walls (11+inches) than AAC walls (8 inches). Therefore, building with an ICF structure will increase the overall dimensions and square footage of the building.
Why Choose Fox Blocks ICFs vs. AAC?
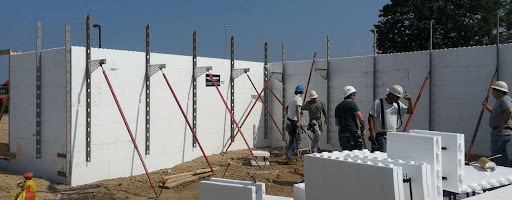
Easy to install, Fox Blocks ICFs provide builders the ideal product for constructing eco-friendly, disaster-resistant, durable structures with excellent indoor environmental quality. Simple to install AAC construction provides some of these features, but they lack the strength to stand up to many natural disasters and moisture resistance, which leads to expensive repairs and unhealthy and structurally damaging mold.
Contact Fox Blocks professionals today to help answer your questions on AAC vs. ICF construction.