
Building Beyond Code with ICF

While it may seem that having to comply with constantly-evolving building codes is just part of doing business in a modern society, that’s not really true.
Building codes can be traced back to 1800 BC, when the Code of Hammurabi (the emperor of Babylon) imposed a death sentence on anyone who built a house that collapsed. In the U.S., building codes go back to the days of George Washington and Thomas Jefferson, who advocated for minimum safety standards to protect citizens from building collapses and other accidents.
While safety is still a primary focus, the scope of building codes has expanded considerably since the days of Hammurabi and Washington. Today’s building codes are increasingly focused on environmental issues: reduced energy consumption, the conservation of natural resources, and the lessening of environmental impacts (such as storm water drainage, erosion, etc.). As a result, architects, designers, and contractors are turning to innovative solutions.
Demand for Energy-Efficient Solutions
You can’t change the laws of physics. Things like heat transfer and air infiltration are just part of the world we live in. So, as code requirements for energy conservation continue to strengthen, the construction industry relies on building material companies to come up with products that mitigate the effects of those natural laws. The improvements gained through products like insulation, reflective roofing and window films have made significant reductions in the the amount of energy it takes to keep a building heated and cooled.
And then there are the innovations that blow right past incremental improvements, setting a new standard for energy-efficient construction. Insulating concrete forms, or ICFs, are a great example of that type of giant-leap-forward innovation. ICFs not only meet the standards for IBC compliance, they blow them out of the water.
ICF's Innovation on Energy-Efficient Design
ICF’s concrete wall systems are reinforced with steel and insulated with a double layer of polystyrene foam, combining strength and energy efficiency in individual units that can be arranged in countless designs.
When the construction industry initially began focusing efforts on energy-efficient buildings, we heard a lot about a material’s “R-value,” or its resistance to heat transfer. What we’ve learned since then is that there’s more to the equation than the R-value of any particular material used in wall construction.
To really determine how energy-efficient a building is, you have to consider three factors: continuous R-value, thermal mass and air infiltration.
Continuous R-value
Continuous R-value is a key attribute of a building’s thermal performance. It refers to how well the wall as a unit resists heat transfer.
This may be different than the R-value of individual components. In a wood frame house, for example, the R-value of the insulation has to be adjusted because of thermal bridging, to include the lower R-value of the wood framing. So, while a builder may use fiberglass batt rated R-19, the R-value of the wall as a whole will be lower.
ICFs are different: the insulation is incorporated into the structural elements of the blocks. Instead of layers of various materials with differing R-values, ICFs provide one continuous and consistent thermal value for the building envelope, exceeding code minimums. In other words, what you see is what you get.
Air infiltration
Over half of the energy lost in a traditional wood frame structure is due to the way heat passes through the various layers: wood framing, fiberglass batt, exterior finish, etc.
As energy efficient as any individual component may be, there’s the potential for heat loss in every gap between layers. Adding blown-in or sprayed-on insulation can reduce infiltration, but it can’t eliminate it completely: wood frame buildings typically have 50% more air infiltration than ICF buildings.
Thermal mass
“Thermal mass” is the scientific term for thickness. Because walls made from ICF blocks are considered mass walls, they delay heat transfer, maintaining a more stable inside temperature despite external heat fluctuations.
In areas where nighttime temperatures are considerably cooler than daytime temperatures, the mass concrete within the blocks can release their stored heat at night, in a process called “heat flow reversal” or “thermal lag.” This considerably reduces the energy needed to heat and cool the building on a daily basis, for the life cycle of the building.
The combination of these three factors creates what’s known as the “ICF effect”: high-performance buildings that require 44% less energy to heat and 32% less energy to cool than comparable wood frame houses.
Improving on Current code Standards
While we seek code-compliance, it’s crucial that building material companies continuing innovating on current industry standards. Many structures built to current minimum code standards are considered safe, but that doesn’t guarantee the building’s resilience after future disasters or stricter codes in the future.
In fact, research shows that designing to exceed code pays off. According to the National Institute of Building Sciences, “specific disaster mitigation strategies that go beyond the requirements of the 2015 International Codes model building codes could save the nation billions of dollars.”
Their 2017 Interim Report found that building designs that “exceed select code requirements can save the nation $4 for every $1 spent.”
ICFs don’t just contribute to code-compliance, however. They contribute to building performance in several ways:
- By contributing to LEED certification.
- By enabling HERS certifications below the national standard for Zero-Energy-Ready homes.
- By providing a healthier enviornment in terms of air quality and acoustics.
- By standing up to even the strongest wind storms.
In other words, when it comes to ICFs and building codes, compliance is just the starting point.
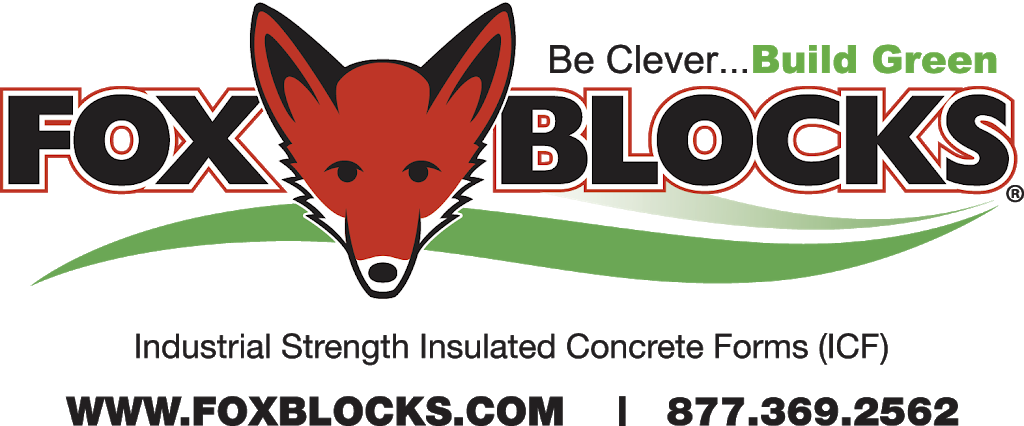