
7 Things to Know About Basement Insulation Code

Basement heat loss accounts for 15 to 30 percent of the annual heat load from a two-story home, and may potentially be higher in a single-story structure. Basement air leakage can occur through windows, penetrations, cracks, and at the top of the foundation wall.
For new construction, adding code-approved insulation on the exterior of the basement walls provides numerous benefits:
Lessens heat loss through the foundation, minimizing thermal bridging
Protects the damp-proof coating from damage during backfilling
Lessens moisture intrusion
Incorporates the foundation into the thermal mass of the conditioned space, reducing interior temperature swings
Minimizes condensation on surfaces in the basement
Saves room space, compared to installing insulation on the interior
A below-grade basement must be able to handle varying climate situations in 3 specific areas — the 2-foot section of the above-grade wall, the first 3-4 feet for frost, and the bottom remainder for the earth temperature. These 3 areas all require different abilities of the basement wall and the insulation to handle: thermal resistance, air pressure, moisture, and condensation.
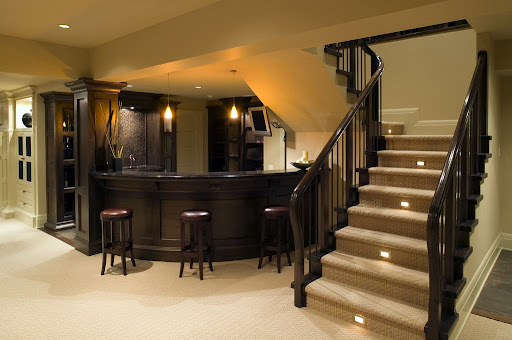
Guidelines for Basement Insulation Codes
Building codes vary significantly between cities, states, and regions, so the information in this post serves only as a general guideline for residential basement insulation codes, and references from Chapter 11 and Chapter 3 of the 2021 International Residential Code (IRC). Chapter 11 provides the minimum design requirements to promote efficient energy utilization in residential homes, including basement walls. The IRC defines a basement wall as 50 percent or more below grade, enclosing conditioned space. Chapter 3 involves building planning.
7 Things to Know About Basement Insulation Code
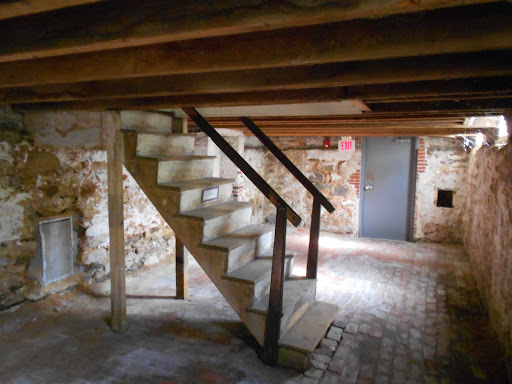
1. Required Protection of Exposed Basement Insulation (N1101.11.1 (R303.2.1))
Applying a rigid, opaque, and weather-resistant protective covering to the exterior of the walls, extending not less than 6 inches below grade, can prevent the insulation’s thermal performance degradation.
2. Basement Wall Insulation R-Value Alternatives (IRC Table 1102.1.3)
The 2021 IRC mandates the minimum insulation R-value requirements for basement walls based on climate zones. The R-value measures an insulation’s thermal resistance, or the ability of an object or material to resist the flow of heat. Generally, the greater the R-value, the better the product will resist heat flow, meaning a warmer house in the winter and more consistent inside temperatures in the summer.
Climate zone 0, 1, and 2, or warm and humid regions, do not require basement insulation.
Climate zone 3 requires either R-5ci on the interior or exterior service of the wall or R-13ci on the wall’s interior side.
Climate zone 4 (except marine) requires either R-10ci on the interior or exterior service of the wall or R-13ci on the wall’s interior side.
Climate zone 4 marine, 5, 6, 7, and 8 requires either R-15ci on the interior or exterior service of the wall or R-19ci on the wall’s interior side, or you can apply R-5ci and R-13ci on the wall’s interior side.
3. Unconditioned Basement Wall Insulation Requirements (N1102.2.8 (R402.2.8))
Unconditioned basement walls do not need insulation if they meet all of the following requirements:
Proper and code-compliant insulated overhead floor and stairway stringer leading to the basement
Insulation of all duct, domestic hot water, or hydronic heating surfaces is not exposed
No HVAC or return diffusers are supplying or serving the basement
Code compliant insulated and weather-stripped doors connecting the basement and the conditioned spaces
Code compliant insulated walls surrounding the stairway and adjacent to the conditioned spaces
Code compliant building thermal envelope separating the basement from the adjacent conditioned spaces
4. Basement Wall U-Factor Requirements (IRC Table 1102.1.2)
The 2021 IRC mandates the maximum assembly U-value requirements for basement walls based on climate zones. The U-Value represents thermal transmittance or heat loss through the basement assembly. The smaller the U-Value, the more effectively the basement wall assembly reduces heat transfer:
Climate zones 0, 1, and 2 require basement wall U-factors of 0.360.
Climate zone 3 requires a basement wall U-factor of 0.091; however, in hot and humid regions, the U-factor can not exceed 0.360.
Climate zone 4 (except marine) maximum U-factor of 0.059.
Climate zone 4 marine, 5, 6, 7, and 8 maximum U-factors of 0.050.
5. Installing Basement Wall Insulation (N1102.2.8.1 (R402.2.8.1))
Install the basement wall insulation from the basement wall's top down to 10 feet below grade or the basement floor (whichever is less).
Homeowners can choose from several basement insulation products, including:
Insulating concrete blocks and forms (new construction)
Sprayed foam insulation
Blanket (batt and roll) insulation
Foam board insulation
Loose-fill insulation
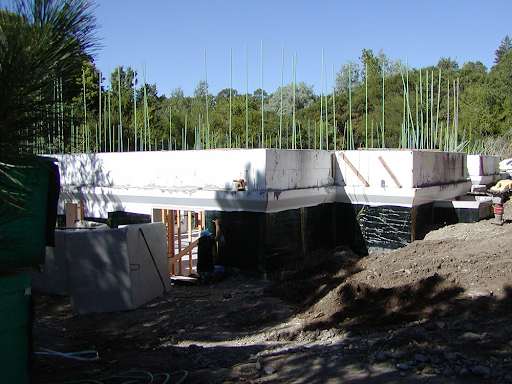
6. Surface Burning Characteristics of Foam Plastic Insulation (R316.3)
The 2021 IRC defines foam plastic insulation's surface burning characteristics (the relative fire performance of specific building products). Foam plastic insulation must meet specific testing criteria related to ignition and fire.
R316.3.1 - Foam plastic insulation less than 4 inches thick
Foam plastic insulation installed 4 inches thick or less must obtain a flame index no more than 75 and a smoke-developed index no more than 450 when tested at the maximum density and thickness meant for use according to the ASTM E84 or UL 723.
R316.3.2 Foam plastic insulation more than 4 inches thick
Four-inch thick or more foam plastic insulation must achieve a flame spread index no more than 75 and a smoke-developed index no more than 450 when tested at a 4-inch thickness according to the ASTM E84 or UL 723, providing end-use approval by Section R316.6 using the intended thickness and density.
Exception:
Four-inch thick or more spray foam insulation requires a flame spread index no more than 25 and a smoke-developed index no more than 450 when tested at 4-inch thick and the intended density. ½-inch gypsum wallboard or approved equivalent must separate the spray foam plastic foam from the home’s interior.
7. Thermal Barrier for Foam Plastic Basement Insulation (R316.4)
The 2021 IRC states that unless allowed in Sections R316.5 or R316.6, you must separate foam plastic insulation (including polyisocyanurate, polystyrene, and polyurethane) from the interior of a building with an approved thermal barrier, like a minimum ½- inch (12.7 mm) gypsum wallboard or the equivalent.
The equivalent thermal barrier material must limit the average temperature rise of the unexposed surface to no more than 250°F (139°C) after 15 minutes of fire exposure (complying with the ASTM E 119 or UL263 standard time-temperature curve). The thermal barrier isolates the foam plastic, ensuring it will remain in place for 15 minutes when exposed to fire.
Exceptions R316.5.1
Masonry or concrete construction does not require a thermal barrier if a minimum of a 1-inch thickness of masonry or concrete separates the foam plastic insulation from the home's interior.
Installing Code-Compliant Basement Insulation with Fox Blocks ICFs
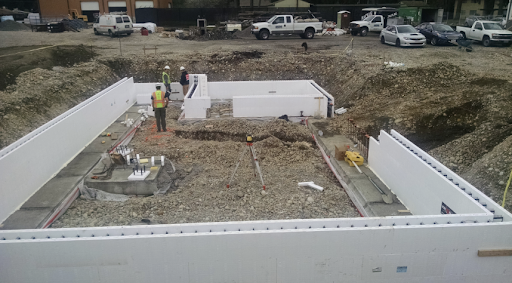
Code-compliant Fox Blocks insulated concrete forms (ICFs), with an R-value of 23, provide an all-in-one wall system, allowing for quick and low-risk basement construction. Fox Blocks combines five-building steps into one, with: air barrier, insulation, vapor retarder, structure, and attachment. The Fox Blocks wall assembly includes a vapor retarder that contributes towards a moisture-resistant basement wall; it still needs a dependable drainage system and waterproofing membrane to insure moisture resistance.
The all-in-one wall system lowers the need to coordinate multiple trades, saving money and significantly hastens project delivery while still achieving the building goals. Fox Blocks ICFs create energy-efficient, durable, and disaster-resistant basements with excellent IEQ.
For more info on code-compliance and R-value vs U-value, contact the foundation experts at Fox Blocks today for more information on basement insulation codes.