
Flexible Construction: Can ICFs be Poured in Multiple Stages?

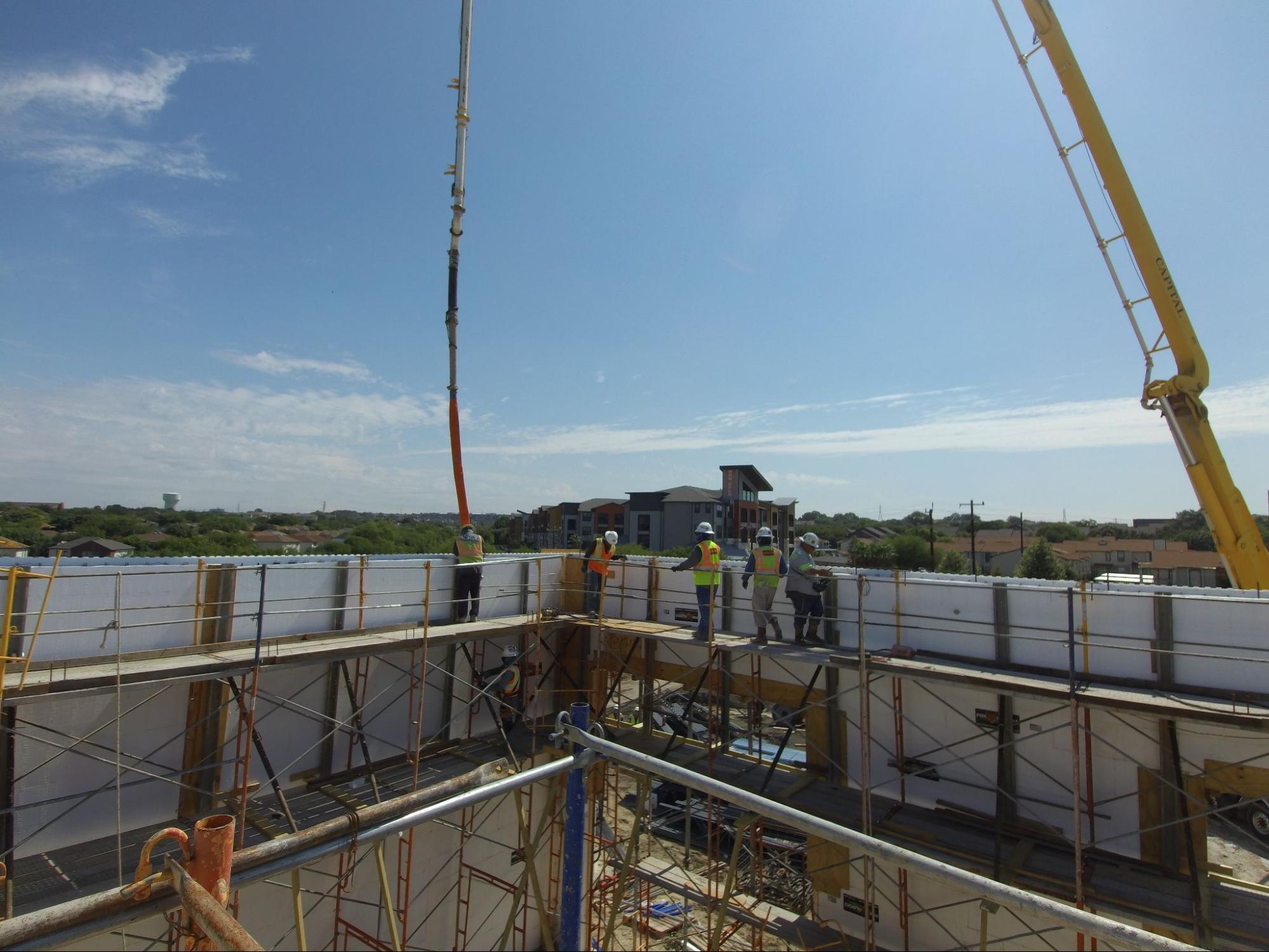
Insulated Concrete Forms, or ICFs, are a welcome game-changer in the realm of construction, that are known for their robustness, resilience, and energy efficiency.
This article explores the possibility of using ICF construction if the concrete is poured in stages, as well as the pros and cons of using that method.
What Are ICFs and What Are They Used For?
Insulated Concrete Forms, often abbreviated as ICFs, are a type of building system designed for enhanced energy efficiency and durability. Essentially, ICFs are modular, interlocking blocks composed of two layers of foam insulation, between which concrete is poured. The blocks act as formwork for the poured concrete, but unlike traditional formwork, they remain in place after the concrete has cured in order to provide added insulation to the structure.
ICFs are predominantly used in the construction of exterior walls for various types of buildings. They are a popular choice for:
Residential homes: ICFs are ideal for constructing energy-efficient and quiet homes.
Commercial buildings: Given their resilience and thermal efficiency, ICFs are often used in commercial structures to reduce long-term maintenance and energy costs.
Institutions: Schools, hospitals, and other institutions benefit from the noise reduction, energy savings, and safety features of ICF construction.
The advantages of ICFs extend beyond energy efficiency and noise reduction. They are highly resistant to fire and extreme weather conditions, which adds to the structural integrity and longevity of buildings constructed using this method.
Benefits of ICFs in Construction
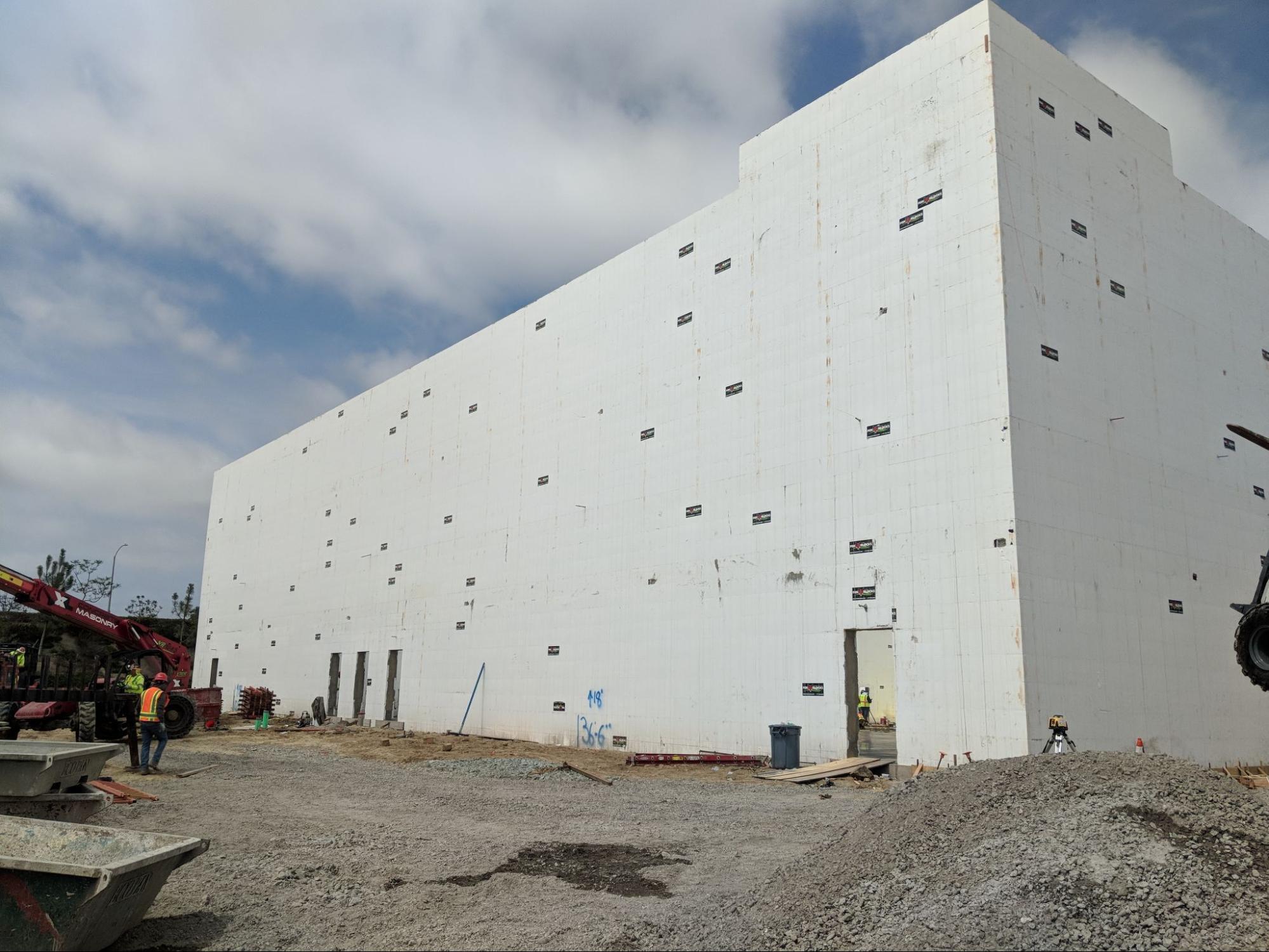
The utilization of Insulated Concrete Forms (ICFs) in construction brings a host of advantages that contribute to the efficiency, durability, and sustainability of the built environment.
Here are the key benefits of ICFs in construction:
Energy Efficiency
ICFs provide superior insulation, which reduces the need for additional heating and cooling systems. This leads to significant energy savings, and reduces the building's carbon footprint and operational costs.
Noise Reduction
The foam insulation in ICFs acts as an excellent sound barrier that provides a quiet and peaceful indoor environment. This is particularly beneficial in urban and densely populated areas where external noise can be a concern.
Disaster Resistance
ICFs are known for their robustness. Buildings constructed with ICFs are highly resistant to extreme weather conditions such as hurricanes, tornadoes, and earthquakes. They also provide superior fire resistance compared to traditional construction materials.
Design Flexibility
ICFs are adaptable and versatile which allows them to be utilized for a wide range of architectural designs and styles. They can be used for both simple and complex designs that offer architects and builders a flexible canvas.
Longevity and Durability
Structures built with ICFs are durable and require less maintenance over time. The concrete core provides structural strength, while the foam exterior prevents the intrusion of moisture, to reduce the risk of mold and deterioration.
Ease and Speed of Construction
ICFs are modular and relatively easy to install, which can expedite the construction process compared to traditional methods.
In a nutshell, the use of ICFs in construction projects brings numerous benefits, such as energy efficiency, resilience, design flexibility, and more. They represent a forward-thinking approach to construction, which is particularly well-suited to our growing sustainability concerns.
Pouring ICFs in Stages
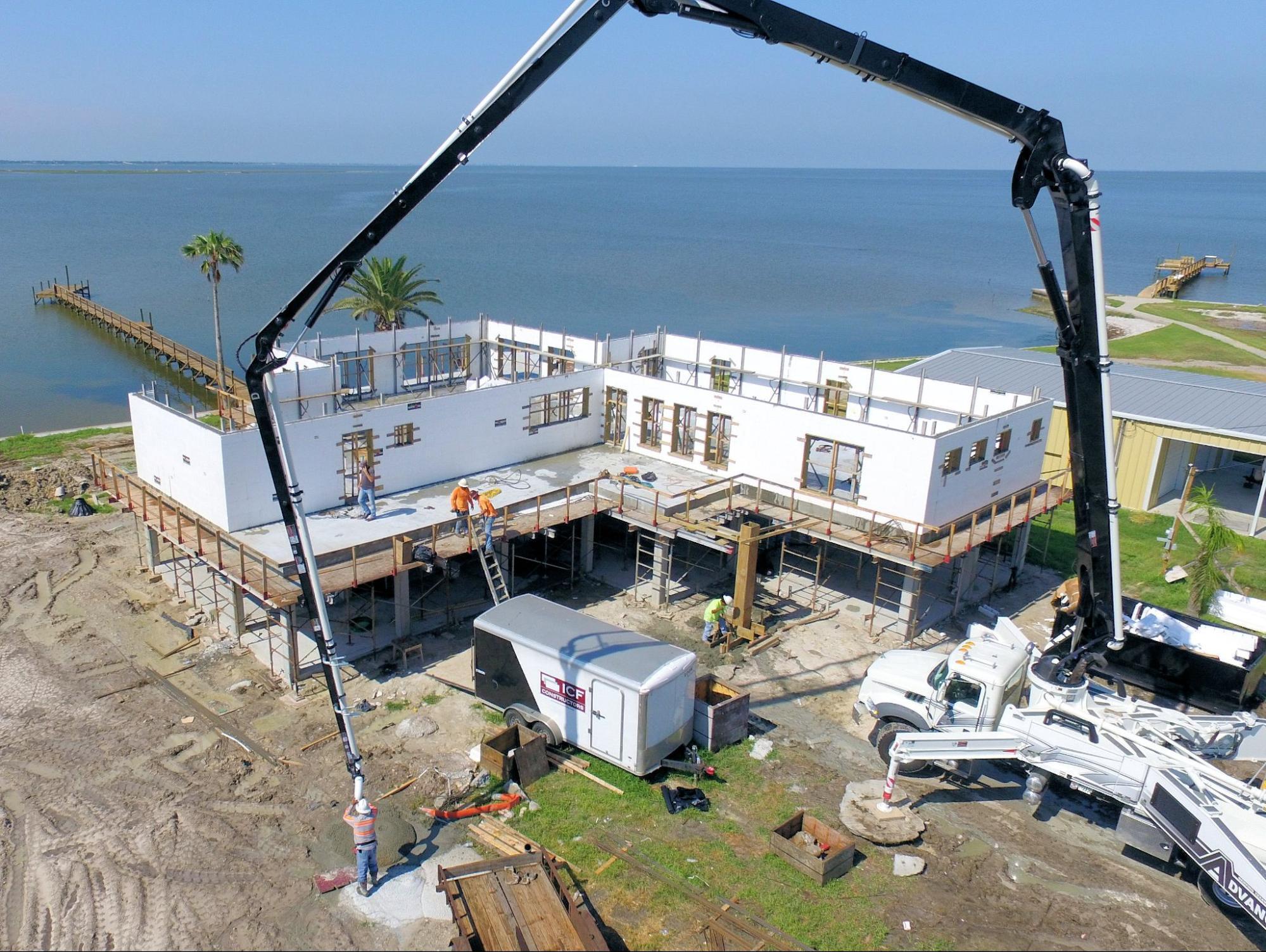
Pouring Insulated Concrete Forms (ICFs) in stages is a widely practiced and recommended method, mainly owing to the control and precision it offers. The process involves placing concrete in the ICF walls in layers or 4 foot lifts and consolidation of the layers. Below grade walls must have the concrete placed in lifts continuously to top of the wall. Above grade walls, also placed in lifts, may be placed with cold joints.
ICFs required a specific concrete mix design with a higher slump and smaller aggregate. Check with the ready-mix supplier. Typically, the concrete is placed from a pump truck.
Here's a basic step-by-step guide to this process:
1. Form Setup: Start by assembling and setting the ICF forms in accordance with the project's blueprint. Reinforcing bars, horizontally and vertically, are typically placed within the forms to provide additional structural integrity, per engineering design specifications.
2. Initial Pour: Begin the concrete pour by filling the first few feet of the ICF forms. The actual height of this initial pour may vary, but it's often around two to four feet.
3. Subsequent Pours: Allow the initial layer of concrete to slightly harden to support the next layer, then continue with the next layer and consolidate each layer. Depending on the linear footage and height of the walls, concrete placement may take three lifts around the perimeter to reach the finished wall height.
The benefits of pouring ICFs in stages include:
Control: The process offers better control over the quality and consistency of the wall. It also allows for regular checks for alignment and form stability.
Prevents Form Failure: By limiting the pressure on the lower forms, this method reduces the risk of form blowouts.
Consistency: It ensures a more consistent curing process, as the entire wall cures at a similar rate.
Preparing for Concrete
Conduct a pre-placement checklist of the walls, alignment, scaffolding and equipment prior to concrete arrival
Assign the crew with tasks for placement, consolidation, safety and any unexpected problems
Discuss the placement plan with the pump truck operator
Conduct a post placement checklist to align and plum the walls.
Pouring ICFs in stages is a tried-and-true method that can yield high-quality, robust, and consistent walls. Fox Blocks Resource library has concrete specifications, and checklists for concrete placement.
Choose Fox Blocks for Your ICF Construction Needs
When you're diving into ICF construction, Fox Blocks is your trusted partner. With our superior range of ICF products, we're committed to providing energy-efficient, resilient, and flexible solutions tailored to your project's unique needs. We offer extensive guidance to master the process of pouring ICFs in stages, fostering a partnership aimed at building lasting, high-quality structures.
Contact us today for more information!