
6 Phases in the Life Cycle of a Construction Project

Understanding the construction project life cycle is essential for effective project management. Each phase, from initiation to project closeout, plays a critical role in ensuring that projects are completed on time, within budget, and to the desired quality standards. This article outlines the 6 phases in the construction project life cycle by highlighting the technical benefits and practical applications of Insulated Concrete Forms (ICFs) to enhance each phase.
What is a Construction Project Life Cycle?
A construction project life cycle refers to the structured sequence of phases that a construction project undergoes from its inception to completion. Each phase is designed to achieve specific objectives by ensuring that the project progresses methodically and efficiently. The life cycle encompasses various stages, each with its own set of tasks and milestones that ultimately lead to the successful delivery of the project.
Phase 1: Initiation
Initiation is the starting point of any construction project. This phase involves defining the project's goals, scope, and feasibility. It includes conducting a feasibility study and creating a project charter. Assembling the project team and identifying key stakeholders are also crucial steps.
Feasibility Study and Project Charter
A feasibility study assesses the viability of the project by considering factors such as budget, timeline, sustainability, resiliency and technical requirements. The project charter outlines the project's objectives, stakeholders, and initial plans.
Phase 2: Planning
The planning phase involves developing detailed project plans, including timelines, budgets, and resource allocation. Establishing a work breakdown structure (WBS) and setting milestones are critical to this phase.
Developing Detailed Project Plans
Creating a comprehensive project plan involves identifying all tasks, assigning resources, and setting a timeline. This plan serves as the roadmap for the project that guides all subsequent activities.
Phase 3: Pre-Construction
In the pre-construction phase, finalizing designs and obtaining necessary permits are key activities. This phase also involves selecting contractors and procuring materials.
Finalizing Designs and Permits
Detailed designs and blueprints are completed, and necessary permits are secured from local authorities. This ensures that the project meets all regulatory requirements.
Phase 4: Execution
The execution phase is where the actual construction work begins. Managing subcontractors, vendors, and daily operations are essential to this phase.
Managing Construction Activities
Effective management of construction activities ensures that the project stays on schedule and within budget. Regular monitoring and adjustments are necessary to address any issues that arise.
Phase 5: Performance Monitoring
Performance monitoring involves tracking project progress against the plan, reporting regularly, and making necessary adjustments.
Tracking Progress and Adjusting Plans
Regular performance monitoring helps identify deviations from the plan early to allow for prompt corrective actions. This ensures that the project remains on track.
Phase 6: Project Closeout
The project closeout phase involves completing final inspections, obtaining approvals, and handing over the project to the client. Finalizing documentation and conducting post-project evaluations are also part of this phase.
Final Inspections and Hand-Over
Final inspections ensure that the project meets all specifications and quality standards. Upon approval, the project is handed over to the client.
Integrating ICFs into Each Phase
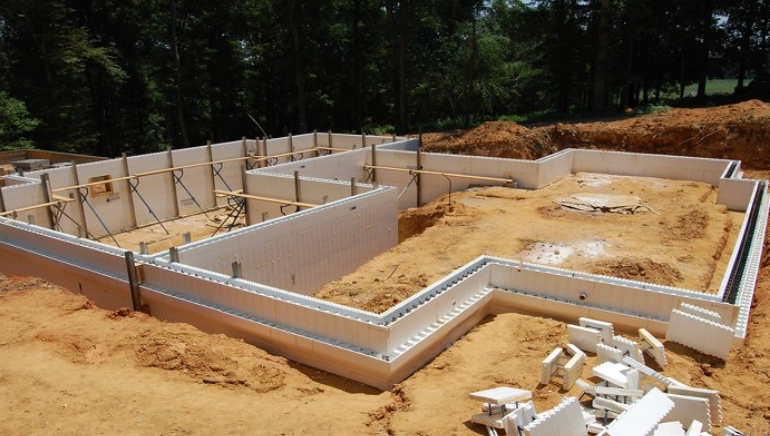
Insulated Concrete Forms (ICFs) are integral to enhancing the efficiency and effectiveness of the construction project life cycle. ICFs are lightweight, interlocking blocks or panels that are made of expanded polystyrene (EPS) foam, which are then filled with reinforced concrete. They provide numerous benefits that streamline processes, improve resource management, and promote sustainability.
Flexibility and Adaptability
ICFs are highly adaptable, which makes them suitable for various stages of residential or commercial construction:
Their modular design allows for easy adjustments in project scope or design, which is particularly beneficial during the initiation and planning phases.
Changes in project requirements can be accommodated without significant delays or additional costs.
For example, ICFs can be easily configured for different building heights and complex architectural designs by providing flexibility that traditional materials often lack.
This adaptability ensures that the project can evolve smoothly as new requirements or challenges arise.
Streamlined Resource Management
Using ICFs simplifies resource management by reducing the need for multiple materials and trades:
This leads to more efficient allocation of resources and minimizes waste and downtime.
ICFs combine structural support, insulation, and vapor barriers into a single product, which eliminates the need for separate installations of these elements.
This integration reduces the number of subcontractors required on-site, minimizes coordination issues, and accelerates the construction timeline.
Consequently, projects using ICFs often see lower labor costs, faster completion timelines and fewer scheduling conflicts, which contributes to overall project efficiency.
Sustainability and Environmental Impact
ICFs contribute to sustainable construction practices by providing superior energy efficiency and utilizing recycled materials.
The insulating properties of ICFs result in buildings with higher thermal performance, which significantly reduces heating and cooling costs.
Additionally, ICFs are often made from materials that include over 40% recycled content, which further enhances their environmental benefits.
Their durability and resiliency means they require less maintenance and have a longer lifespan compared to traditional building materials, which reduces the need for frequent repairs and replacements.
This longevity translates into lower long-term environmental impact and cost savings for building owners.
Furthermore, the energy efficiency of ICF buildings reduces their carbon footprint to support broader sustainability goals in the construction industry.
Enhance Every Phase of the Construction Life Cycle with Fox Blocks
Fox Blocks Insulated Concrete Forms (ICFs) are designed to optimize every phase of the construction project life cycle, from initiation to closeout. By incorporating our ICFs, you can significantly enhance efficiency, reduce costs, and improve the overall quality and sustainability of your construction projects.
Contact us today for more information!