
Energy Modeling as an ICF Design Tool

The rising demand for more sustainable buildings has made green construction increasingly profitable and desirable in the U.S. and the global construction market as well. Leaders in Energy and Environmental Design (LEED)-certified projects (internationally recognized green building certification program) in the U.S rose from 296 in 2006 to over 69,066 in 2019, a trend that is expected to continue.
Building energy models (BEM) are a vital tool for helping today’s engineers, architects, and builders keep up with the increasing demands for high-performing, energy-efficient homes and buildings.
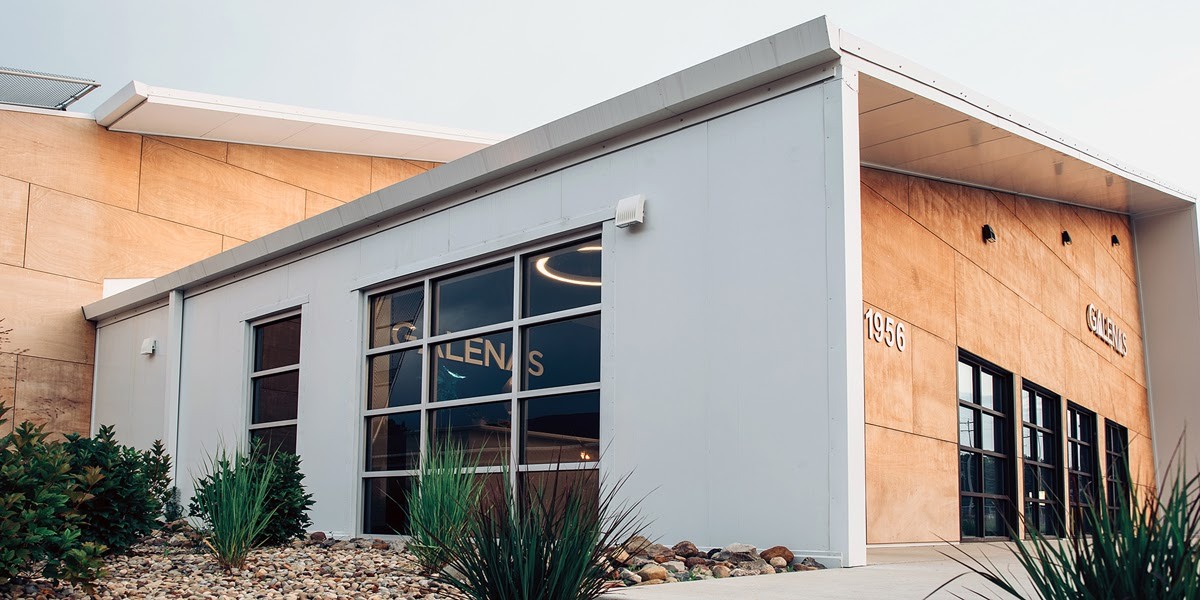
What is Energy Modeling?
Energy modeling uses mathematical equations to estimate the possible energy expenditures of a building. An energy model adds known variables, such as construction materials, specific site characteristics like daylighting, occupant’s requirements, and average local climate conditions into the equations to determine unknown variables, like energy performance and cost.
Designers can use the model to tweak the variables to improve the overall performance of the system. For example, enhancing the building envelope's insulation or facing the front of a house south would improve a home’s energy efficiency.
Why Use a Building Energy Model?
Since the first computers in the 1950s, engineers have used steady-state calculations (models) to assess heating and cooling loads of a building based on its design, with the goal of minimizing energy consumption.
Today, green-sustainable builders, architects, and engineers rely on BEMs to conduct pre-design and comparative analysis of a building’s systems and strategies' potential performance. BEMs strive to optimize energy performance, ultimately achieving net-zero energy use. Energy modeling enables the entire building team to make integrated design decisions based on a full understanding of how systems interact, along with the costs, both during and after construction.
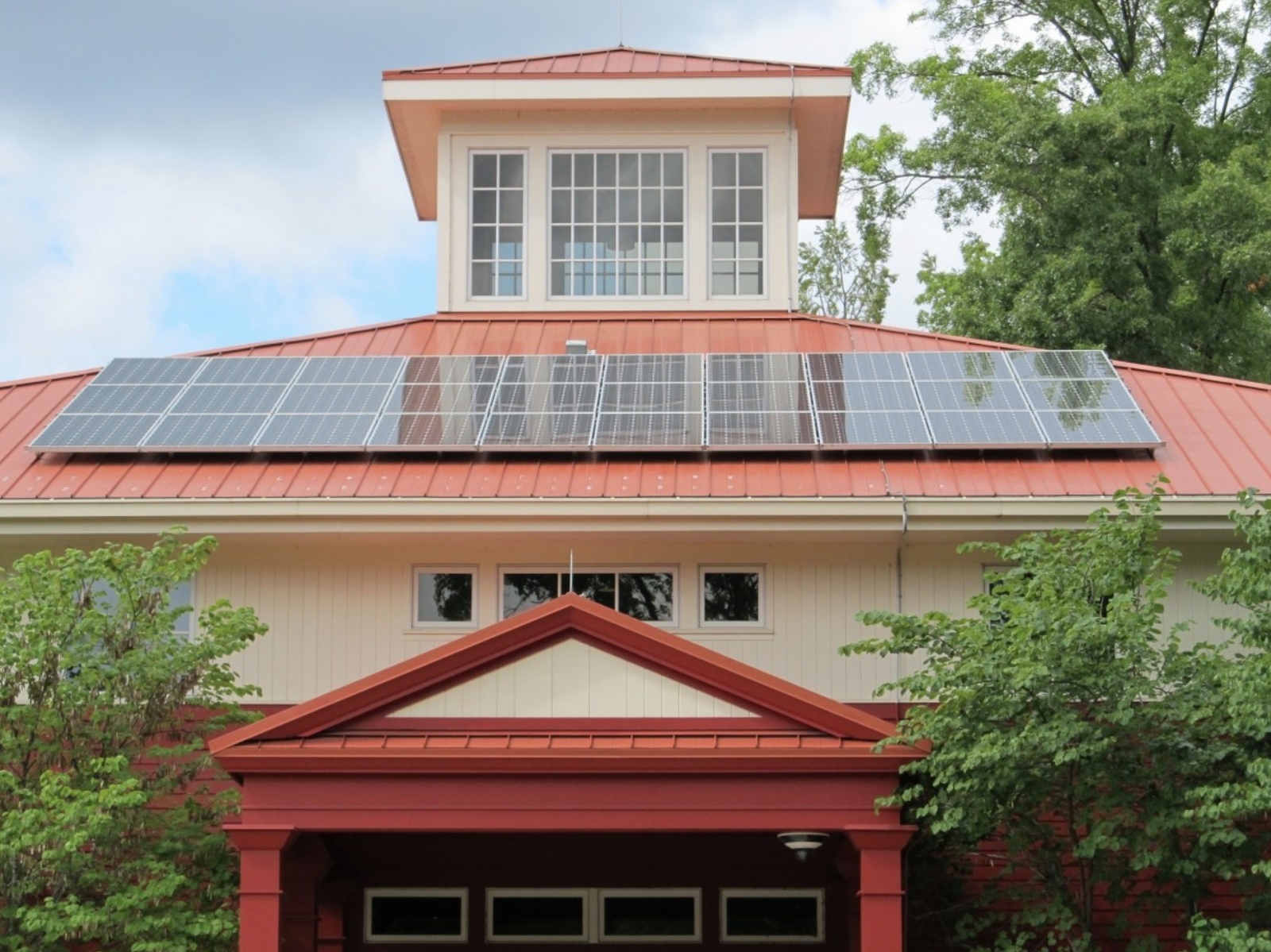
The Benefits of Early-Stage Building Energy Modeling
Building teams utilizing BEMs early in the design phase can maximize the building's energy efficiency by avoiding designs that undermine the structure's performance. BEMs done in the pre-design phase of a building project can reduce energy use by 45 percent. Other benefits of early-stage building energy modeling include:
- Architects and engineers can use BEMs to help clients achieve their energy-efficiency goals and provide an accurate estimate of the structure’s energy use and cost.
- Builders and architects can use energy models as a means to ensure a design produces code-compliance and green building certification requirements for LEED, ASHRAE’s Building Energy Quotient (bEQ), Home Energy Rating System (HERS) Index, or Green Globes.
- BEM can help to qualify for tax credits and utility incentives.
- BEM can determine when the returns on efficiency no longer provide cost-effective savings. For instance, installing solar panels costs 15,000-$25,000, and it can take 7 to 20 years to cover the initial cost. Therefore, it may not be the right choice if you plan to move before paying off the panels.
Energy Modeling as a Design Tool for the Wall System
The early design phase of construction provides the ideal time to compare the energy-efficiency of the wall system of the building envelope. Using an energy model and keeping all other equation variables constant, architects and builders can insert different wall systems into the equation, like insulated concrete form, wood frame, and non-mass walls. The model calculates energy efficiency and cost for each wall system. Doing this early in the design phase allows you to choose the most efficient, short- and long-term, cost-effective wall system for your building project.
Energy Modeling Study Proves ICF’s Superior Energy Efficiency
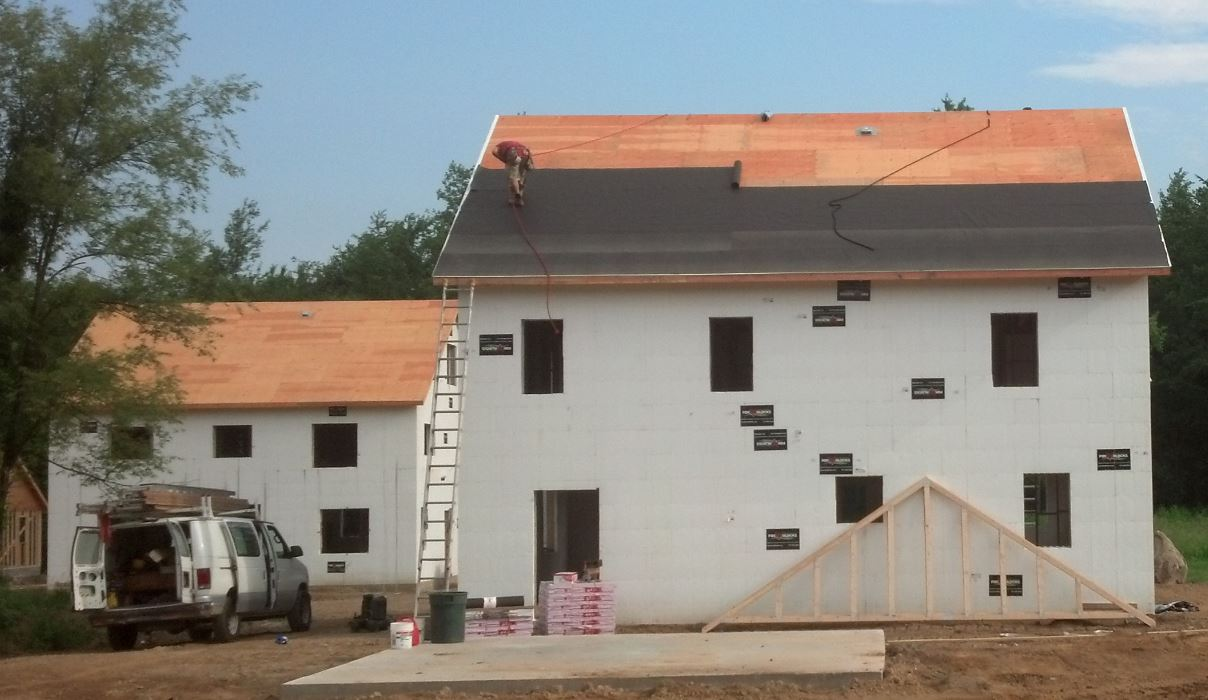
A study using energy modeling proved the superior energy-efficiency of ICF walls over wood-frame and non-mass walls. The study compared five contemporary designed 2,450-square-foot houses in locations representing different climates in the U.S. Energy simulation software utilizing the DOE 2.1E calculation engine performed the modeling.
The total energy used for the ICF walls was 5 to 9 percent lower than wood-framed houses and 8 to 19 percent below non-mass walls that met IECC requirements. Homes with ICF walls provide further savings by reducing the required heating, ventilation, and cooling (HVAC) system capacity. Total system capacity for houses with ICF walls was between 16 percent to 30 percent less than houses with walls IECC compliant and 14 percent to 21 percent less than wood-framed homes.
Fox Blocks ICF Improves the Outcome of Building Energy Modeling
Fox Blocks recommends you ask your architect or engineer to use building energy modeling in the early design phase to maximize your new building or remodel project's potential energy-efficiency. Furthermore, including Fox Blocks ICFs as the wall system variable in an energy model will improve estimates for the building or home's energy expenditures compared to other wall systems.
Easy to install Fox Blocks ICFs surpass ASHRAE/ANSI 90.1 energy code requirements creating high-performing buildings and homes with superb moisture resistance and energy efficiency. Fox Blocks solid continuous monolithic concrete wall, with a perm rating of less than 1.0, controls moisture intrusion and stops the growth of mold, rot, and mildew. Fox Blocks continuous insulation, with an R-value of 23, creates an airtight building envelope with better performance than wood- or non-mass-construction.
Please contact Fox Blocks ICF professionals for more ideas on how you can improve your building’s or home’s energy performance with building energy modeling.