
House Framing 101 - How to Select the Best Framing Option for Your Home

For framing a home, Fox Blocks ICFs provide all the advantages of wood, CMU, and steel, but none of the problems. Fox Blocks are quick and easy to install saving on the initial building costs. They are energy-efficient, disaster-resistant, and durable, which saves on long-term expenses compared to wood, CMU, and steel framing methods.
House Framing 101 - Selecting the Best Framing Option for Your Home
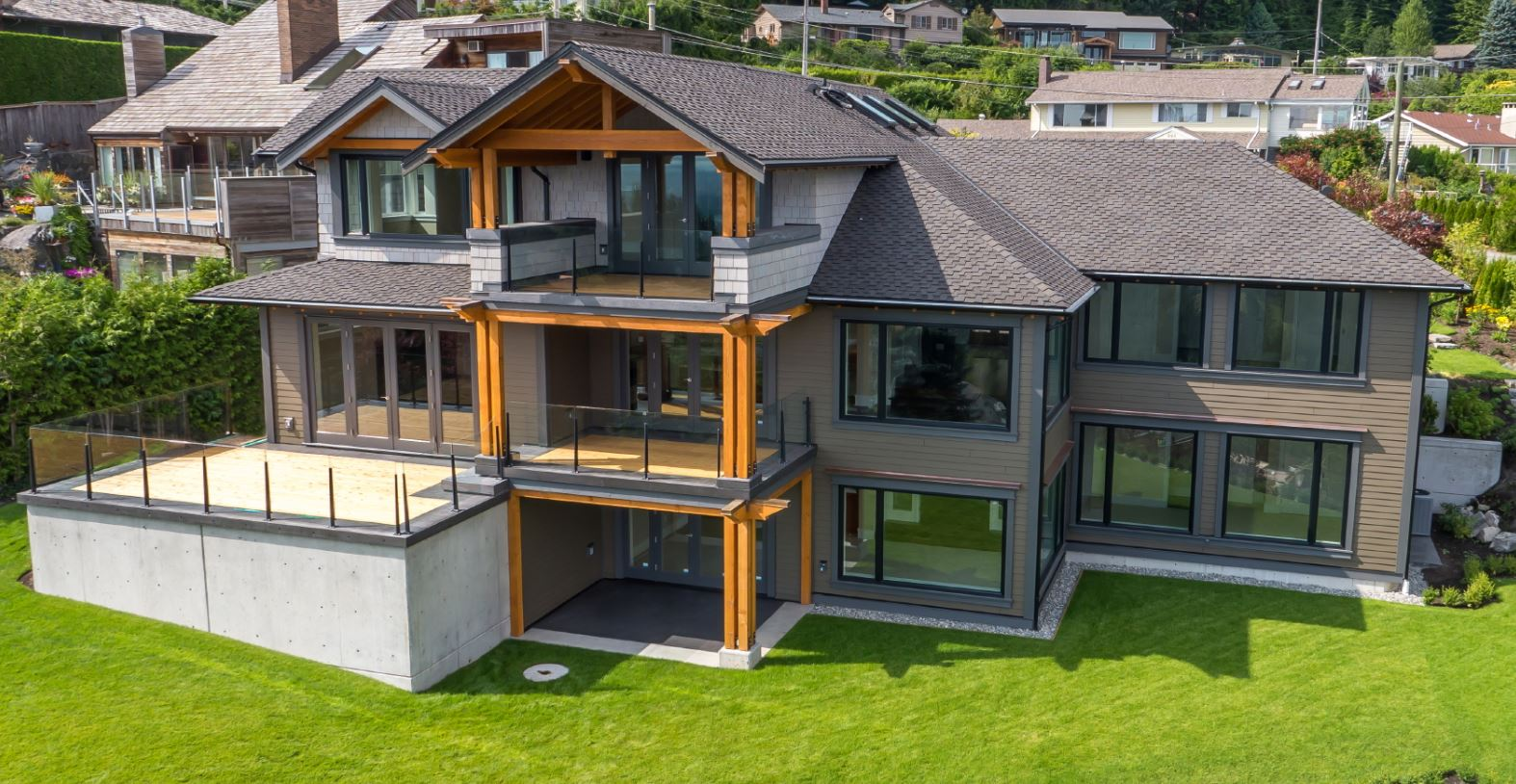
The framing of a house provides the structure that gives a home its shape, and provides the outer shell for the exterior coverings. Selecting the best framing option for your home involves evaluating upfront construction costs and long-term expenses, along with each method's strengths and weaknesses.
Comparing the Short and Long-Term Costs of House Framing Methods
The most cost-effective framing material for a new home project must consider the initial material and labor costs and the long-term cost of ownership and operating expenses to the homeowner.
Upfront Framing Expenses
The upfront building expenses of framing materials and labor vary by location, which makes it difficult to compare the costs of different framing methods. For most regions of the U.S., wood and concrete block framing both offer a slightly less costly framing method than ICF and steel framing.
Fox Blocks ICFs save on upfront costs due to the all-in-one wall assembly that combines five construction steps into one, structure, air barrier, insulation, vapor retarder, and attachment. This saves money and time because it quickens construction by eliminating the need to synchronize multiple trades.
Long-Term Costs
When comparing framing methods, homeowners must consider the long-term expenses, such as maintenance, utility bills, insurance and repairs. Does the framing method contribute towards an energy-efficient, durable-, disaster-, and pest-resistant house?
- Energy-efficient framing reduces utility bills:
- Energy-efficient Fox Blocks ICFs, with an R-value of 23 and high thermal mass, exceed ASHRAE/ANSI 90.1 energy code requirements.
- Homes constructed with ICF exterior walls require 32 percent less energy to cool and 44 percent less energy to heat than wood-framed homes.
- Wood and steel framing promotes thermal bridging, which lowers the effective R-value of a home.
- Fox Blocks homes with energy efficient windows and doors and quality roof insulation will provide a high-performance Net Zero Ready home.
- Durable framing lowers the long-term costs of maintenance and repair:
- Durable Fox Blocks provide a solid continuous monolithic concrete wall with a perm rating below 1.0. This feature controls moisture intrusion and prohibits the growth of mold. Unhealthy mold leads to costly maintenance and repair bills.
- Steel and concrete blocks also resist moisture.
- The susceptibility of wood to moisture can lead to expensive repairs and maintenance.
- Disaster-resistant framing minimizes the costs of repairing and rebuilding after a natural disaster:
- Wind-resistant Fox Blocks, along with steel and CMU framed homes, lessen the need for costly repairs or even rebuilding after a severe wind event, like a tornado or hurricane.
- Construction of a wind-resistant wood-framed home costs 25–30 percent more than standard wood-frame construction.
- Fox Blocks ICFs produce fire-resistant homes, unlike wood and steel homes.
- When a fire occurs, the combustibility of wood can make it challenging to reduce the spread of flames.
- Steel can lose its strength at high temperatures, so a steel-framed home may buckle or even collapse during a fire. Also, steel acts as an active conductor of heat and can ignite adjacent materials, which may cause flames to spread rapidly to other areas of a home.
- Termite-resistant walls preserve a home's integrity and eliminate expensive maintenance and repairs:
- Concrete and steel resists termites. Wood and Fox Blocks ICF both require treatments like an application of Polyguard Products, Inc. 650 XTM or 650 XTP membranes to prevent termite damage.
Breaking Down the Strengths and Weaknesses Between Four House Framing Options
Besides the initial and long-term costs of a framing method, homeowners should compare their strengths and weaknesses.
1. Insulated Concrete Forms (ICFs)
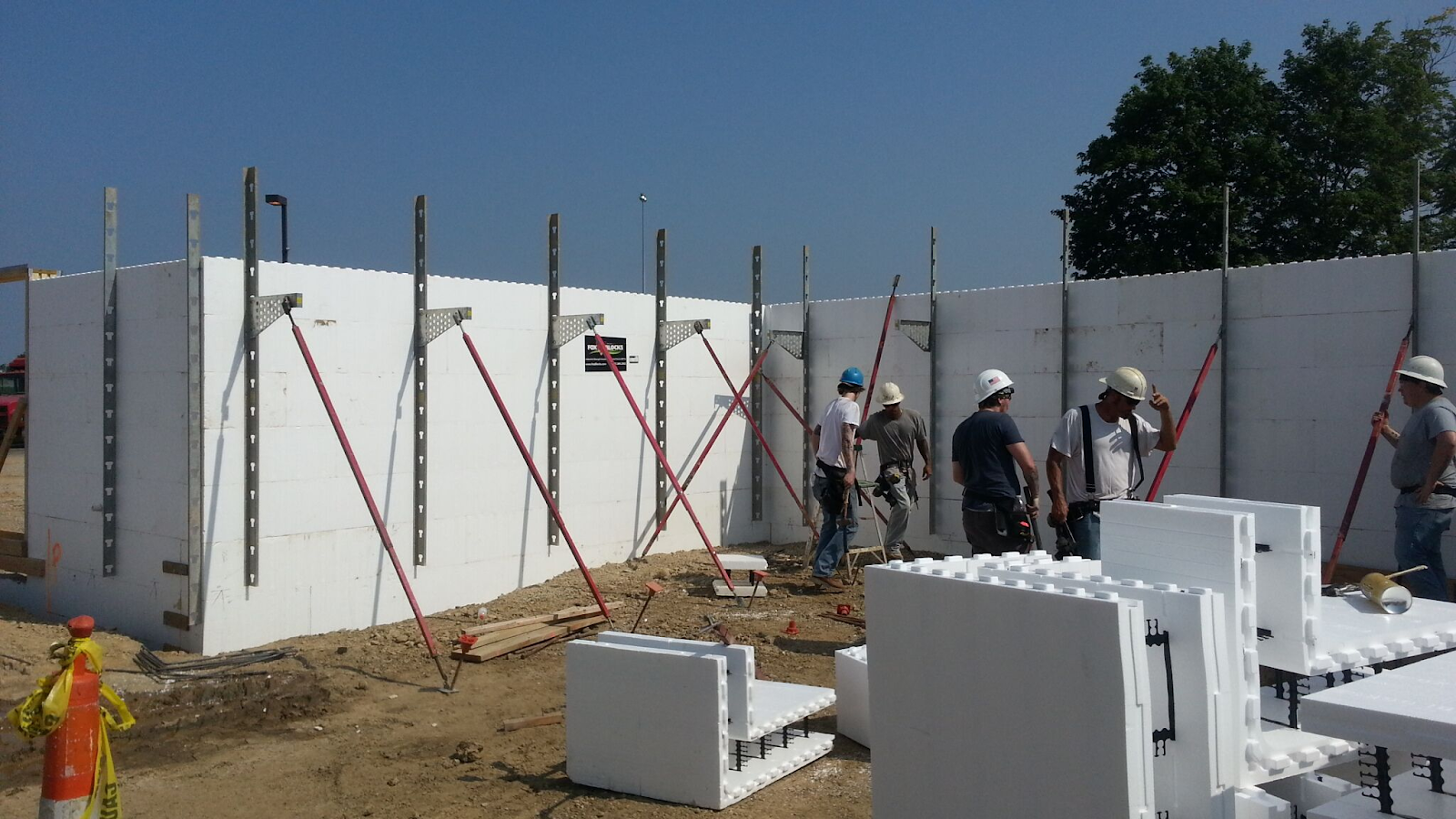
ICF wall systems produce strong, energy-efficient, durable, and disaster-resistant framing for a house. Building an ICF wall involves pouring reinforced concrete into hollow panels (made of expanded polystyrene or EPS), with reinforcing bars. Before pouring the concrete, workers dry-stack the interlocking units. After the concrete cures, the inner and outer continuous layers of EPS insulation panels produce a permanent exterior framework for the home.
Strengths of an ICF Wall System
- Moisture-resistant, it controls water accumulation in the wall interior, which ensures a durable and healthy house.
- Creates long-lasting and disaster-resistant homes.
- Energy-efficient, airtight homes lessen energy use and reduce utility costs.
- The lightweight nature allows for secure handling so contractors can build regular or tall wall heights, above or below grade, quickly, safely, and efficiently.
- ICF construction can proceed in adverse conditions such as freezing temperatures and rain, which saves money on hoarding, temporary heat and costly weather delays.
- Thick and solid walls create acoustically, pleasing homes.
- One contractor can install below and above grade walls ready for finishes.
Weaknesses
- Only qualified and experienced contractors should pour the concrete into ICF walls because concrete poured too rapidly can burst through the polystyrene panels.
- Fox Blocks provides training for the installation of the ICF and placement of concrete.
2. Light Wood Framing
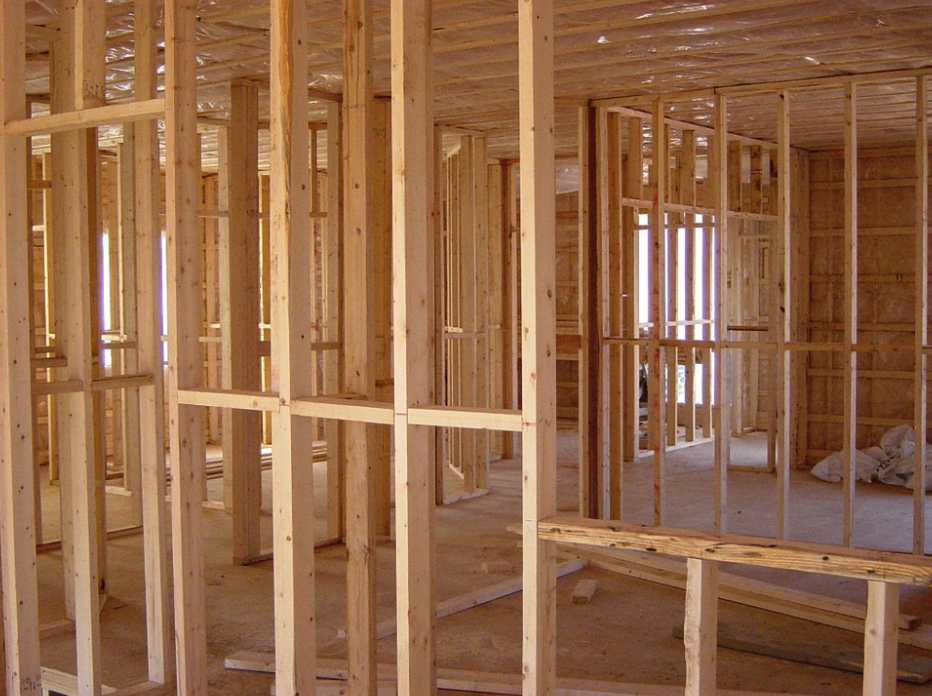
In the U.S., builders often use wood composed of softwood trees like fir, pine, and spruce. Manufacturing of the planks involves sawing and machine-planing to standard widths and lengths.
Wood framing remains the most popular building method for homes in the U.S. In fact, in 2018, builders constructed 778,000 wood-frame homes - representing 93% of all new houses built.
Strengths of Light Wood Framing
- Builders can easily access light wood because of the availability of cut lumber and machine-made nails.
- Light wood framing allows for quick construction because contractors can easily lift every component with no heavy tools.
- Light wood allows for design flexibility.
- Renewable light wood helps the environment.
Weaknesses
- Homeowners must spend 25 to 30 percent more to construct a wood-framed house with the strength to withstand severe winds flooding and earthquakes, compared to conventional building methods.
- Energy codes are requiring wood framing to be thicker to add more insulation. This means 2x6 or 2x8 framing or even double offset 2x4 stud exterior walls.
- Combustible wood needs design methods that prevent fires and also limit the spread of the flames.
- Lacks moisture-resistance, which can lead to unhealthy mold and expensive repairs.
- Termites eat wood, which degrades a home's integrity.
3. Concrete Masonry Units (CMUs) Framing
In 2018, builders constructed 59,000 concrete homes - 7 percent of the completed housing market. Most of this construction (98 percent) occurred in the South.
CMU’s manufacturers use materials like Portland cement, water, and stone or quartz aggregate to make CMUs. Contractors can choose solid or hollow CMU's, with two or three cores, in a range of shapes.
The Strengths of CMU Framing
- Fireproof CMUs act as a firewall between structures or rooms.
- Moisture-resistance stops the growth of mold.
- Pest-resistance improves a home's durability.
Weaknesses
- Do not contribute insulative value to an energy-efficient house.
- Today's wall systems require CMU construction to include more components, layers, and steps - all of which takes more money and time, compared to CMU projects in the past.
- Masonry industry is lacking skilled labor.
4. Steel Frame Construction
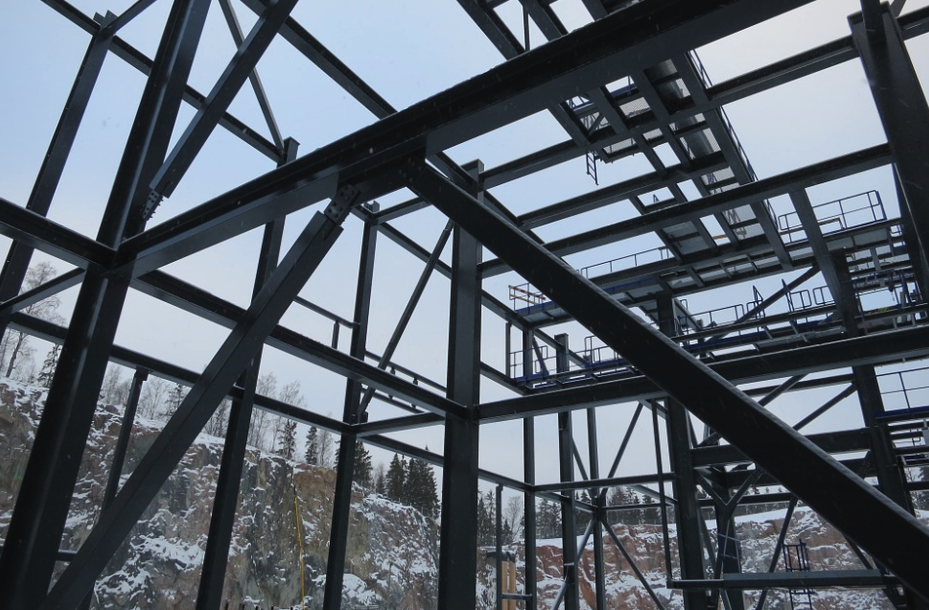
Steel-framed houses represented less than half a percent or 3000 of the finished houses in 2018 - two-thirds of these homes were built in the South, with the other one-third built in the West.
Strips of galvanized steel in cold rolling machines produce the steel studs for framing. Load-bearing walls require studs with heavier gauge metals than steel studs for non-load bearing walls.
The Strengths of Steel Framing
- Moisture does not affect galvanized studs; therefore, steel studs won’t warp or rot and can remain sturdy and straight for the lifetime of the home.
- Termite-resistant steel doesn't require pest control features.
- Strong steel framing stands up to severe wind events.
- Workers can easily carry hollow and lightweight steel studs.
- Steel studs lack volatile organic compounds (VOCs).
Weaknesses
- High temperatures, like during a fire, diminishes the strength of steel, which makes it prone to buckling. Steel also conducts heat, so materials near the steel studs can ignite, causing flames to spread to other areas of a house.
- A steel framing system may cost 15 percent more than wood framing.
- Workers find it challenging and hazardous to cut steel studs.
- The conductivity of steel causes thermal bridging.
Fox Blocks offers new homeowners a solution to all of the weaknesses associated with wood, CMU, and steel framing options. Fox Blocks saves on upfront expenses by reducing the labor and time needed during construction, expediting completion and occupancy timeframes, and long-term costs by lessening energy use and minimizing maintenance, repair, and replacement expenses.
Please contact Fox Blocks professionals for more information on why ICF is the best framing option for your new home.