
How Long Does It Take to Frame a House?

Framing is the foundation of a home’s structure that creates the framework for walls, floors, and the roof. The time it takes to complete this phase depends on the framing method and several other factors.
This article explores the differences between traditional wood framing for exterior walls versus Insulted Concrete Form (ICF) wall construction, and sheds light on how each method influences construction speed and efficiency.
Wood Framing: A Traditional Method with Changing Timelines
Wood framing is the most common method for residential construction. It involves using lumber to build the walls, floors, and roof structure to form the skeleton of the house. The time required for wood framing can vary significantly depending on several conditions.
Key Factors Influencing Exterior Wall Framing Timelines
Size and Complexity
A small, single-story house can be framed in about 2-3 days, while larger, multi-story homes may take 2-3 weeks or more depending on the complexity, corners, openings, etc.
Labor Availability
The number and experience level of workers also impact the framing timeline. A skilled crew working full-time will finish framing much faster than an understaffed or less experienced team.
Potential Delays
External factors like material availability, site accessibility, and weather conditions (rain or snow, temperature) can halt progress when framing with wood, which adds unpredictability to the process.
Typical Steps in Wood Framing
Installing subfloors
Build and erect wall frames, including exterior and interior walls
Add exterior sheathing, internal blocking, wind bracing and load path columns.
Adding roof trusses and sheathing for structural integrity, hurricane tie-down straps
The basic wood framing creates the skeleton of the home, there is still much work required to make the exterior wall assembly complete with interior and exterior insulation, vapor retardant, weather barrier, air sealing, etc. These applications require more materials and possibly additional labor, and sub-trades to be coordinated to complete this process.
More and more contractors are looking to alternative building systems to expedite labor, meet or exceed rising building and energy code requirements and elevate their business by producing high-performance and resilient homes. ICFs meet all these requirements and more.
Accelerating Construction with ICF
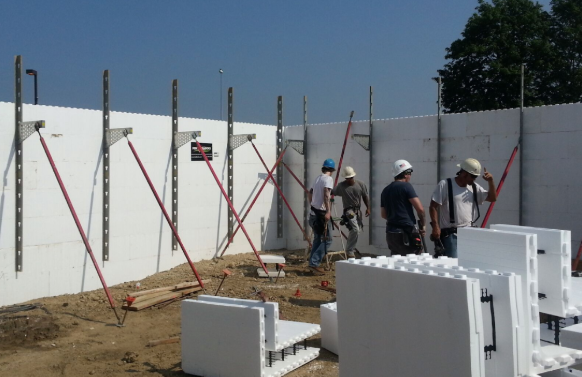
ICF not only speeds up the construction process, it also simplifies several stages compared to wood framing. Here’s how ICF enhances construction efficiency:
All-in-One Framing and Insulation
ICF blocks come with built-in insulation, meaning that once the walls are erected, they are already insulated. This integrated approach eliminates the need for additional steps like installing insulation, vapor retardant, air and weather barriers, which is required in wood framing. Homeowners benefit from time efficiency and superior energy savings, with R-values at a minimum of R-23 and air tightness well below 3 ACH, HERS ratings below 50, which makes ICFs as a one product exterior wall assembly, significantly more energy-efficient than typical wood-framed walls.
Labor Efficiency
With ICF, fewer workers are required to erect the walls due to the simplicity of stacking foam blocks. Concrete pouring (6" concrete core for above grade walls) can be done quickly, to further reduce the need for a large labor force, which in turn means less downtime and faster overall completion.
Understanding how weather impacts construction timelines is crucial when comparing wood framing and ICF methods.
Weather and Delays Comparison
Both wood framing and ICF construction can be affected by weather, though in different ways. Wood framing is highly vulnerable to delays caused by rain or snow, because moisture can warp materials and stop work. In contrast, ICF is much less affected by weather since its materials are moisture-resistant, which allows construction to proceed without significant delays. ICF construction can proceed year round and is not influenced by winter temperatures. Construction and concrete placement can occur in cold temperatures. This provides contractors the ability to work year round to produce high-performance ICF foundations and homes.
It’s important to examine the specific timelines associated with ICF construction to understand its efficiency compared to traditional methods.
ICF Construction Timelines
Once the ICF foundation and subfloor or slab on grade foundation is installed, the above grade ICF walls can be completed in just a few days, depending on the size and design of the house. The actual process of stacking the blocks and pouring concrete is often completed within a week. Since the ICF system handles 6 in 1 at once (structural support and resiliency, double layer of insulation, vapor, air and weather barriers, strapping for interior and exterior finishes), it eliminates the need for additional construction steps. Once the windows are in and the roof is in place, the house is insulated, weather tight and for the next phase much sooner than with traditional wood framing.
To fully appreciate the advantages of ICF, it's essential to compare the post-slab timelines of wood framing and ICF construction.
Comparing Post-Slab Timelines: Wood Framing vs. ICF
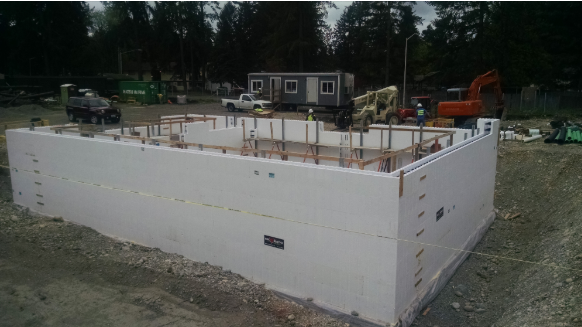
Once the concrete slab has been poured, the differences in post-slab timelines between wood framing and ICF construction become more evident. The timeline for both methods can vary depending on the size and complexity of the project.
Wood Framing
Post-slab, wood framing typically takes anywhere from 1 to 3 weeks to complete. Smaller homes with straightforward designs can be framed in about 1-2 weeks, while larger or multi-story homes may require more time. The process involves erecting walls, installing roof trusses, and adding insulation, all of which are completed in separate stages. This segmented process often results in delays due to weather conditions and labor availability.
ICF Construction
In contrast, ICF framing after slab installation can be completed much faster due to its integrated design. The ICF process combines framing, insulation, and structural integrity into a single step that allows walls to be erected in just a few days. For many residential projects, ICF walls can be completed within a week or less. Additionally, ICF blocks are moisture-resistant, which means that they can be installed even in less-than-ideal weather and temperature conditions to significantly reduce potential delays.
Evaluating the long-term benefits of ICF reveals its efficiency and durability as significant advantages for homeowners.
Long-Term Benefits of ICF: Efficiency and Durability
ICF construction offers several advantages beyond the initial build time.
The use of the double layers of insulation and the thermal mass of the concrete leads to improved air tightness and overall energy efficiency, reducing energy consumption by up to 50% monthly, compared to traditionally framed homes. This is due to the superior insulation provided by ICF walls, which prevents heat loss in winter and retains cooling in summer.
ICF walls also provide increased durability by resisting moisture damage, fire, and pests that commonly affect wood-framed structures. This makes ICF a long-term investment reducing maintenance costs over the lifespan of the home.
When selecting a framing method, it’s important to consider various factors in building the whole wall assembly that influence the decision between wood framing and ICF.
Choosing the Right Framing Method
When deciding between wood framing and ICF construction, several factors must be considered, including cost, climate, and desired project timeline. While wood framing remains a popular choice for smaller, simpler projects, the innovative of ICFs provide significant advantages in terms of speed, durability and energy efficiency, particularly for larger homes or homes built in areas prone to extreme weather conditions.
For homeowners looking to reduce construction delays and ensure long-term energy savings, ICF is a superior solution compared to traditional wood framing. However, those on a tight budget or building in favorable climates may still find wood framing to be the better option, whereas with ICFs the initial upfront costs are paid back monthly by the enhanced utility cost savings that continue for the life-time of the home.
Build Faster and Stronger with Fox Blocks ICF
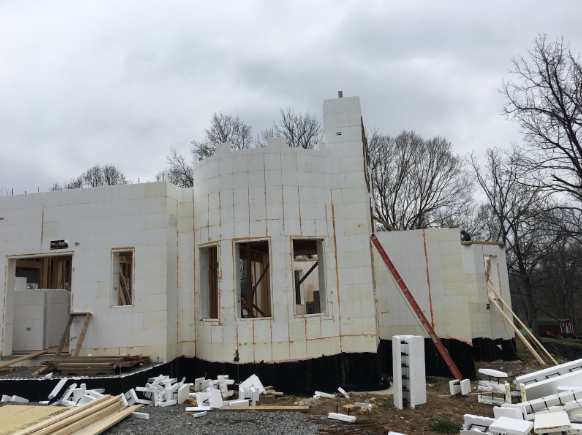
Fox Blocks offers advanced ICF solutions that streamline the construction process while also providing high performance, energy-efficient, durable homes. By choosing Fox Blocks, you can minimize construction time, reduce energy costs, and enhance your building's resilience.
Contractors can be trained free as an ICF Primary Installers on the Fox Blocks Integrated Learning Center website.
Contact us today for more information!