
How Much Does it Cost to Frame a House?

When you build a house, framing will take the biggest bite out of your budget; however, costs vary significantly based on your home’s design and material choice. Typically, framing represents nearly 20 percent of your total construction costs. While most contractors include framing in the overall construction costs, we advise obtaining a framing cost estimate before you begin construction, when you can still tweak your home’s design to lower the price to frame. We also suggest you consider how the framing materials will affect your home’s long-term costs: will it provide energy savings, lower maintenance, and protect against natural disasters? All features can save you money on utility bills, maintenance, and repairs.
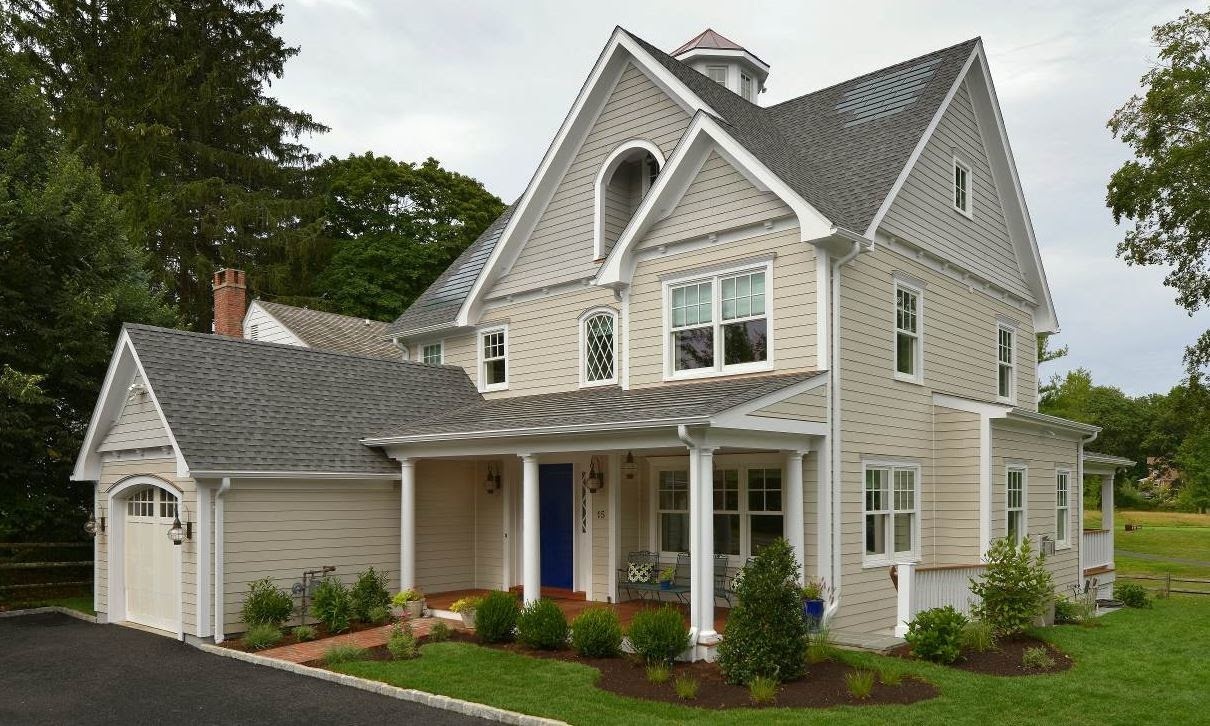
Fortunately, Fox Blocks insulated concrete forms (ICFs) offer a cost-effective framing solution over expensive steel and wood. Fox Blocks save on upfront expenses by reducing the time and labor required during construction. Furthermore, energy-efficient, durable, and disaster-resistant Fox Blocks save on long-term costs by lessening energy use and minimizing repair, replacement, and maintenance costs.
What is House Framing?
Framing gives shape to your home. Framing involves assembling the structural outline that holds together the walls, siding, windows, doors, and roof. It also conceals the electrical wiring and plumbing and provides the shell for the outer coverings. Notably, a durable, long-lasting home requires a well-constructed frame.
Estimating Framing Costs for a New House
Framing requires a specialized team, including a general contractor or structural engineer, to create perfect walls and exactly parallel joists, ensuring the strength and integrity of the frame. Estimating framing costs depends on several of your new home’s features.
The bigger and more complex a home’s design, the more you will pay for framing per foot2.
Specialty details to the home’s design like house soffit and fascia, tall windows, and high ceilings will increase the material and labor costs for framing.
Framing costs vary depending on the framing material, such as wood, concrete block, steel, and insulated concrete forms (ICFs).
How Much Does it Cost to Frame a House?
The cost to frame a house depends on the home’s design and size and the framing product ﹘ all factors that impact framing labor and material costs. Four framing product options include wood, steel, concrete block, and insulation concrete forms (ICFs).
1. Light Wood Framing Construction
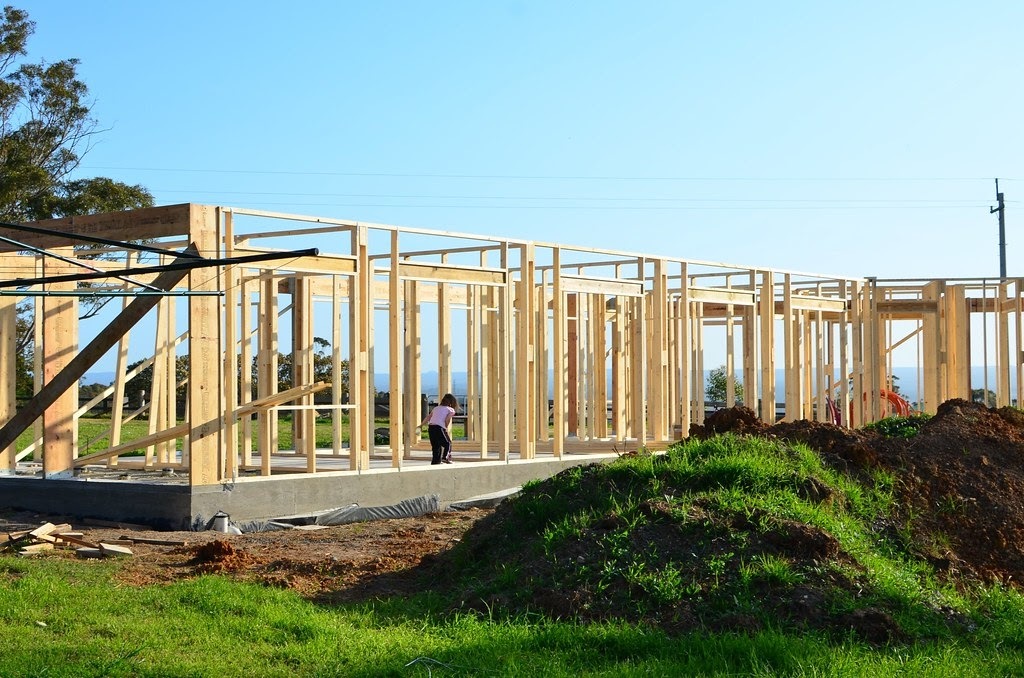
Initial Costs
Wood framing remains the most popular construction method for single-family homes (90 percent) in the U.S. However, COVID-19, Canadian tariffs, severe wildfires, and increasing demand have put supply-side constraints on lumber, increasing the price by over 200 percent. Unfortunately, experts forecast lumber prices to continue to rise through 2021, further increasing framing costs. Escalating lumber prices may lessen the popularity of using wood for a home’s frame.
The cost to frame a house with wood ranges from $1 and $5 per foot2. So, a 2000 foot2 house requires between $6000 and $12,000 in lumber materials; add 15 to 22 percent for sheathing. Expect to pay $20+ per hour for labor to frame a wooden home.
Long-Term Costs
Wood-frame homes can cost homeowners a lot of money in the long run. Low thermal-mass wood does not provide as much energy efficiency as buildings constructed with high thermal mass products like ICFs, leading to higher utility bills. Of concern, the vulnerability of wood to moisture can lead to damaging mold and expensive repairs. Termites eat wood, causing thousands of dollars in damage. Moreover, building a wood-framed home with the strength to resist extreme wind events, flooding, and earthquakes challenges most builders and can cost 25–30 percent more than standard construction.
2. Steel Frame Construction
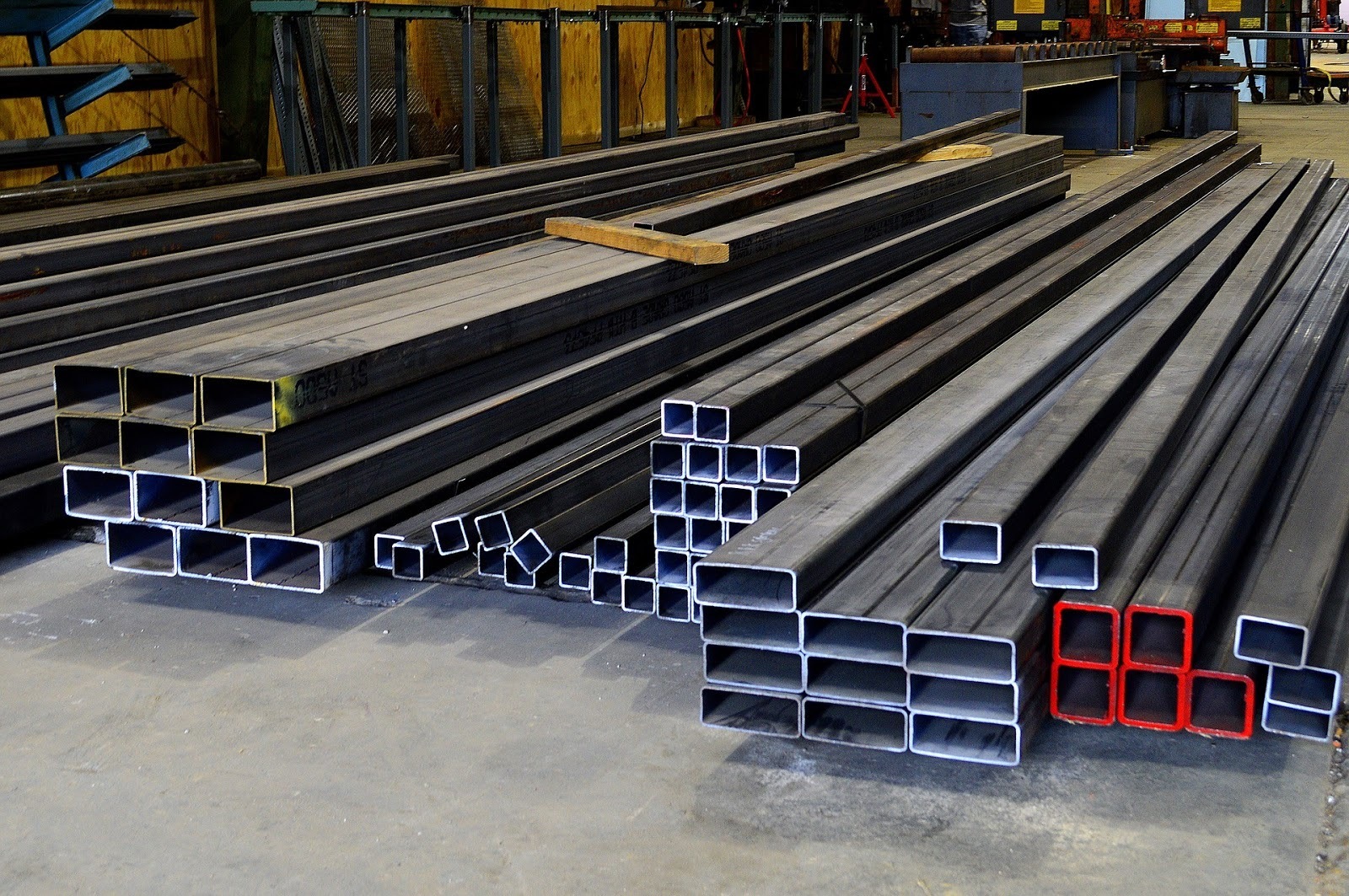
In 2019, steel-framed home construction represented less than half a percent, just 3000 houses. The lack of popularity of steel-frame construction may be due to the limited availability of less common dimensions of steel studs, which can slow the building's progress. Also, contractors find it difficult and hazardous to cut steel studs.
Initial Costs
The cost to frame a house with steel ranges from $9.50 to $11 per foot2, or about $19,000 to $22,000 for a 2,000 foot2 home. Labor to steel frame a home will run slightly more than a wood-frame home at $21.50 per hour, partially because taping a drywall screw into a steel stud requires experienced carpenters. Studies find that a steel-framing system can cost 15 percent more than a wood-framing system.
Long-Term Costs
Disaster-resistant steel frame construction will protect a house against dangerous wind events, saving homeowners money on repairs. Durable steel studs resist moisture and termites so will not warp or rot, remaining straight and sturdy for their lifetime.
However, the conductivity of steel framing leads to thermal bridging, increasing the energy cost for the homeowner. Of concern, steel-framed homes lose strength at high temperatures, like during a fire, making the steel prone to buckling and even collapse. Steel also conducts heat, so materials near the steel studs may ignite, causing flames to spread rapidly to other areas of a house.
3. Concrete Block Construction
Concrete block concrete masonry units (CMUs)) construction grew 258 percent between 2009 and 2019, doubling its market share from 5 to 10 percent. In the south, 17 percent of all homes now use concrete. The driving factors for the increasing interest in concrete construction include hurricane-related building codes and historical acceleration of lumber prices, beginning in 2018 and continuing into 2021.
Initial Costs
A concrete block house costs four to ten percent more to build than a wood house. The added expense comes from modern wall systems requiring concrete block construction to include more features, extra layers, and additional steps taking more time and money compared to projects several decades ago.
Long-Term Costs
Durable concrete block framing offers moisture, fire, and pest resistance, saving homeowners money on costly repairs. However, the R-values of concrete blocks range from 2 to 3, which does not contribute significantly to an energy-efficient home.
4. Insulated Concrete Forms (ICFs) Construction

Between 2021 and 2026, builders can expect a CAGR of around5 percentfor the ICF market due much to the demand for energy-efficient and disaster-resistant houses, along with the reduced construction time with ICF. Notably, the highest market share in the ICF market globally occurs in North America, a situation likely to continue through 2026.
Initial Costs
Before 2018, studies found ICF constitution added about 3 to 5 percent to the purchase price compared to a wood frame home ﹘ about $9000 to $15000 for a $300,000 new house. However, with the significant increase in lumber, steel, and labor costs, this figure no longer applies.
Since 2020, the rise in lumber price has added more than $24,000 to the average new single-family home price and nearly $9,000 to a multifamily home.
Furthermore, since August of 2020, domestic steel prices have risen more than 160 percent.
Of concern, in 2021, experts predict labor costs to increase between 2 percent and 5 percent., further increasing the cost to frame a new home, particularly when framing with labor-intensive concrete block, steel, or wood.
ICF avoids costly wood and steel volatility, helping builders more accurately estimate building costs, ensuring a reasonable profit. Framing your home with quick, lightweight, and easy-to-install ICF wall systems further saves money because it does not require expensive lumber and steel or many of the skilled tradesmen or women needed for concrete block, wood, and steel construction. Furthermore, ICF construction can proceed in adverse conditions such as rain, saving money on costly delays.
Long-Term Costs
ICFs offer many long-term saving advantages to homeowners. Energy-efficient, airtight ICF homes reduce energy use and utility costs. Significantly, the durability and strength of ICF create long-lasting and disaster-resistant homes, minimizing maintenance and repair expenses.
How Fox Blocks Can Help Save on Framing Costs
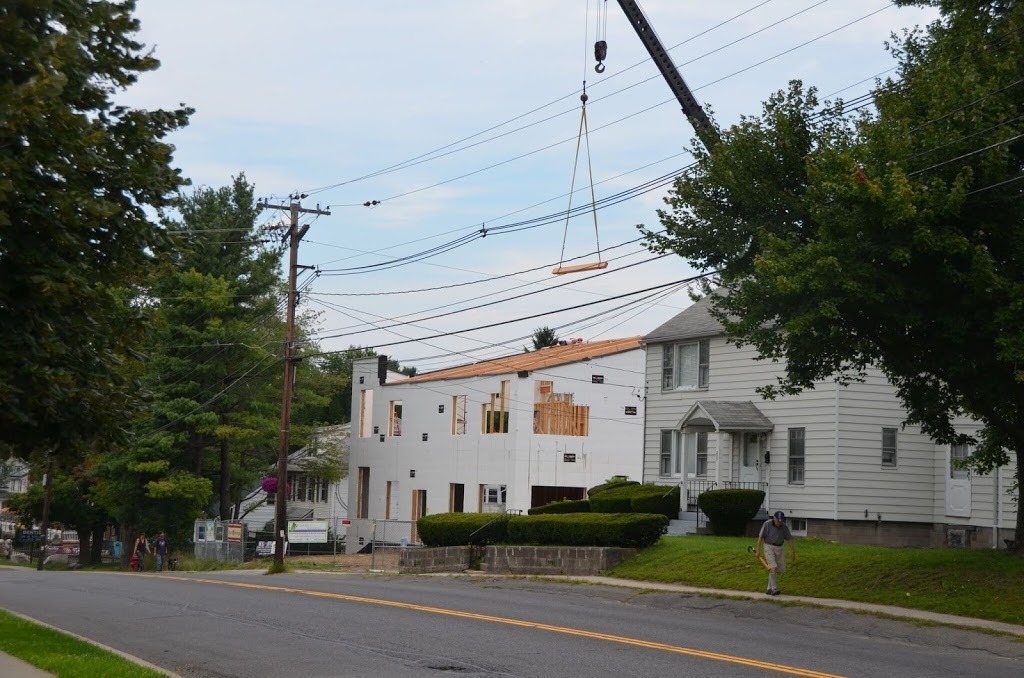
Framing a home with Fox Blocks ICFs offers a superior and cost-effective method over wood, steel, or concrete block. Easy, safe, and quick to install ICFs save on labor costs compared to other framing methods. Notably, the skyrocketing material costs of lumber and steel erase the cost advantage they once had over ICF. ICF also meets the demands of many of today’s new homeowners: energy efficiency, disaster-resistance, and durability — all vital features that will save homeowners money in the long run.
How much does it cost to frame a house? Contact Fox Blocks professionals today to learn why ICF offers the best solution for framing your new home.