
ICFs Make Home Ownership Attainable for Young Adults and Seniors

Young adults, first-time homebuyers, and seniors, many with low and fixed incomes, need affordable, relatively small housing with manageable monthly and annual costs.
Unfortunately, a shortage of low-cost houses has reached a critical level in the U.S, trapping many younger and older people in costly rental units or oversized homes, pushing some back to their parents' homes, or curtailing downsizing.
Insulated concrete forms (ICF), like Fox Blocks, are an excellent building solution for quickly and simply building affordable housing with manageable long-term costs.
Compared to traditional wood construction, ICF offers first-time homebuyers and downsizing seniors superior energy-efficient, low-maintenance, durable homes, ensuring lower utility, maintenance, and repair costs.
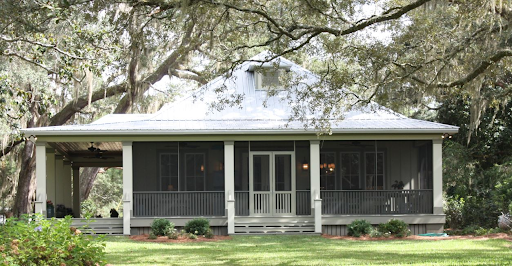
Today's Housing Crisis ﹘Learning from the Past
Post-War Housing Crisis
In the mid-1940s, the U.S. experienced a critical housing shortage due to a slowing, if not halting, of construction during the depression and WWII, leaving nearly 2,900,000 veterans and their families without adequate and available housing. The situation led to increasing home prices, all-time high rents, and a tripling of evictions. Lack of housing and high rents left many young couples and seniors living in substandard housing without updated amenities like electricity and plumbing or in their parent's or children's basements and attics. Sound familiar?
In 1946, Congress passed the Veterans' Emergency Housing Act calling for significant government involvement in housing production, mainly controlling the cost and manufacturing of vital materials and providing loans through the Reconstruction Finance Corporation. The government set the goal to build quickly, moderately, and low-priced up-to-date homes and apartments with modern amenities (electricity, plumbing, etc.). This task challenged traditional home builders and prompted a shift to modular home construction.
During the 1940s, like today, modular home construction was an efficient and lower-cost solution to construct quality, up-to-date, durable homes more quickly than traditional building methods.
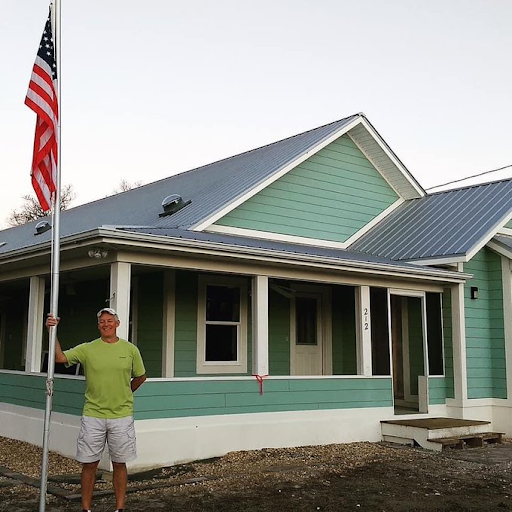
What Today's Housing Crisis Has in Common with the 1940s
Although not driven by the same factors, today's housing crisis has much in common with the 1940s.
Like the 1940s, current housing prices and rents have skyrocketed due to a low inventory of homes. In 2021, the average sales price for a home in the U.S. reached $408,800, nearly doubling the cost in 2020 of $207,000, shutting out many young adults, first-time home buyers, and seniors from the housing market. Of concern, median incomes have not kept up with the high cost of housing, pushing 52 percent of adults under 30 to live with their parents, exceeding the previous high of 48 percent in 1940. In 2021, a 30-year-old makes a median income of $40,560, rising to $50,001 by age 35. 21 years ago, a man's median income was $42,128; for women, it was only $28,116. Thus, over the past 20 years, escalating housing costs, combined with stagnant median incomes, have left many young adults without affordable housing.
Moreover, in the 1940s, builders had to ensure all new houses had modern amenities, like indoor plumbing and heating, unlike many older structures still used for housing.
Today's builders face a similar challenge, only this time it involves constructing more energy-efficient, durable, and safe homes compared to many houses built in the past.
What's Causing the Current Housing Shortage?
Today's housing shortage has escalated the cost to buy or rent a home, resulting in a housing deficit at the end of 2020 of 3.8 million units, an increase of about 52 percent since 2018. The lack of affordable and available houses particularly impacts young adults looking to buy their first new home, and seniors needing to downsize.
We attribute several situations to the current historically low inventory of new and existing affordable homes for sale for new buyers and seniors: a slowdown in construction, labor and material shortages, and COVID-19.
Decline in Construction
In 2020, builders only constructed 65,000 moderately-priced, entry-level homes (less than 1,400 ft2), contributing to a five-decade low in the supply of moderate housing. The long-term decline in the construction of entry-level, single-family homes began in the 1980s, when interest rates significantly increased from 8.9 percent to 12.7 percent, making housing more expensive, leading to a decline in demand and supply. In fact, in the late 1970s, new construction of entry-level, single-family homes averaged 418,000 units per year. After the rise in interest rates, this rose to 100,000 units per year.
Lack of Labor
Today, it takes longer to complete construction projects due to a lack of qualified construction workers. The U.S. Labor Bureau reported 321,000 vacant construction jobs as of April 2019 in the U.S. Some blame the shortage of skilled workers on difficulties in recruiting a new generation of workers and a slow down in immigration. Currently, 88 percent of contractors report moderate to high difficulty finding skilled workers, with 87 percent expressing concerns about the skill levels of workers.
Increasing Material Prices
Despite significant drops in framing lumber prices (640 USD/1000 board feet) since a peak high in May 2021 of 1682 USD/1000 board feet, overall material prices rose 19.9 percent over the past 12 months, with a record year to date increase of 13 percent. During the same period in 2020, the year-to-date increase was only 1.1 percent. Furthermore, The average change in the building materials PPI (producer price index) between January and July was +1.2 percent from 2015 through 2019 — less than one-tenth the gain so far in 2021.
Significant contributors to increasing material costs include steel (up 10.8 percent in July 2021), softwood (up 71.9 percent since January of 2020), and gypsum products (up 15.8 percent year to date). In contrast, ready-mix concrete prices did not change in July after increasing 1.1 percent in June 2021.
COVID-19's Impact on Construction
COVID-19 has significantly impacted the construction industry, although contractors express optimism for the future.
According to the Q2 2021 U.S. Chamber of Commerce Commercial Construction Index, 72 percent of contractors report construction delays due to the pandemic, an 8 percent drop from the same quarter a year ago.
Forty-six percent of contractors report concerns about product availability, up 13 percent from the same quarter last year. When COVID-19 began, lumber mills closed or slowed, anticipating a decline in the demand for lumber. However, the opposite happened — home starts increased due to low mortgage interest rates and the need for new homes, along with a surge in home remodeling.
Twenty-eight percent of contractors report increases in worker shortages due to COVID-19.
ICFs Offer a Quick Solution To Today’s Housing Crisis
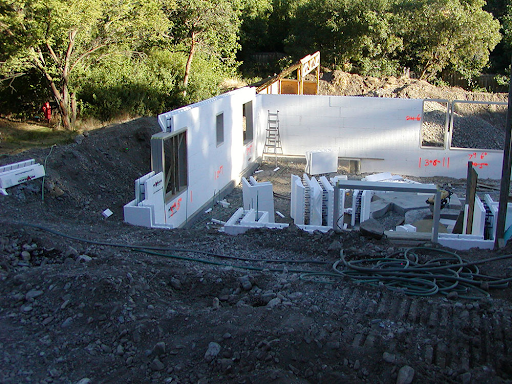
Today, like the 1940s, the current housing crisis mandates an urgent need to quickly build affordable and modern homes, specifically for first-time homeowners and seniors needing to downsize. However, with no immediate solutions to labor and material shortages and issues associated with COVID-19, builders must consider materials and methods that provide a more efficient way to construct single and multi-family unit homes than wood-frame construction.
ICF construction is a modern solution to quickly building affordable houses, similar to modular structures of the 1940s. High-performing ICF homes also provide modern amenities that today's homeowners need and demand: superior energy efficiency, durability, and safety — all features that save homeowners money on utilities, maintenance, and repairs for the lifespan of the home.
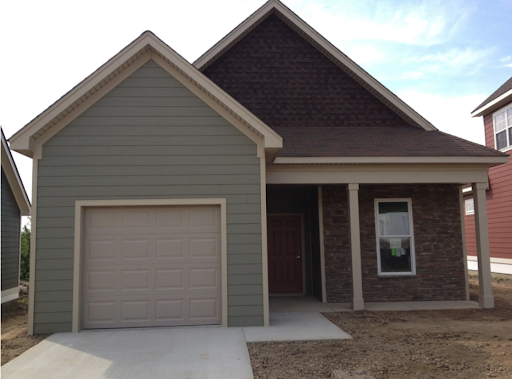
Making Home Ownership Attainable for Young Adults and Seniors with Fox Blocks ICF
Fox Blocks ICFs are a superior product for quickly building new affordable housing, whether a small single home or multi-family unit building for young adults and seniors. Energy-efficient Fox Blocks creates homes with good indoor environmental quality, pest resistance, and protection against natural disasters. ICF homes provide manageable long-term expenses.
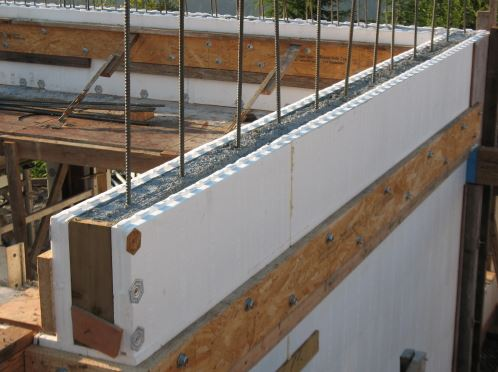
Fox Blocks ICF construction reduces construction time over traditional stick-built or concrete masonry unit (CMS) home construction. ICF construction completes in just one step, framing, continuous insulation, furring attachments, and air and vapor barrier. A small team of trained ICF builders can install ICFs for a single-story house in one day - pouring the concrete on the second day. Contractors can frame and wrap a home in just two days, making it ready for the roof and inside and outside finishings. In addition, ICF construction eliminates the need for caulking or sealing, and interior and exterior barriers. ICF subcontractors can quickly install plumbing, electrical, and HVAC because of the ease of cutting the foam.
Fox Blocks provides CI with an R-value of 23, producing an airtight building envelope, reducing energy use, and saving money.
Fox Blocks also create a solid continuous monolithic concrete wall with a perm rating of less than 1.0. A feature that controls moisture intrusion, stopping the growth of unhealthy and structurally damaging mold, further saving on maintenance and expensive repairs.
Termite-Resistant Fox Blocks lack organic material, which pests like termites eat. However, for waterproofing and termite protection, Fox Blocks recommends Polyguard Products, Inc. 650 XTM or 650 XTP membranes.
Disaster-Resistant Fox Blocks with steel-reinforced concrete can withstand tornado and hurricane winds of over 200 MPH and projectile debris traveling over 100 MPH.
Fire-Resistant Fox Blocks obtain a fire-resistance rating (ASTM E119) of 4 hours for the 6-inch blocks and 2 hours for the 4-inch blocks.
Get in touch with the Fox Blocks professionals today to discuss how ICF construction can make homeownership attainable for young adults and seniors.