
Is ICF Construction Worth the Cost for Commercial Buildings?

ICF construction for commercial buildings has skyrocketed over the past few years. ICF benefits ranging from sound insulation to durability to building strength and disaster resistance have piqued a lot of interest for builders and architects. But it has some scratching their heads, mistakenly thinking ICF is more expensive and then wondering, “Is ICF construction cost worth it?”
At the end of this article, you will have a clear understanding of ICF construction ROI and feel confident that Fox Blocks ICF is a great commercial solution for your next project compared to other materials on the market.
ICF Uses in Commercial Construction
There has been a 30% annual growth in ICF commercial construction, quickly making it one of the fastest expanding building systems in the United States and Canada. A large reason behind is this is the wide range of applications and uses ICF provides for commercial construction.
ICFs are currently used to build Pre-K-12 education buildings, gymnasiums and auditoriums, upper education buildings, student housing, theaters, municipal and federal buildings, DOD buildings, worship centers and faith-based buildings, hospitality-lodging, retail and restaurants, multi-family residential and mixed-use buildings and so much more. It has a versatility that many other building materials don’t have, along with immense benefits to save on costs and add protection.
Cost of ICF
Compared to Steel
For many years, builders have used steel in construction because of its initial low price. However, businesses need to consider total capital costs and long-term expenses before selecting steel as their first choice. Most concerning, steel buildings provide only an exterior structure. They need added costs of separate cladding, insulation, fireproofing measures and corrosion-protection methods. Steel construction plus the added layers required to finish bring the overall cost on par with ICF construction.
Compared to Wood
Today, capital costs for ICF above-grade wall systems compare closely with that of wood-framed commercial construction. Twenty years ago, ICF construction was around 5-10% more than wood-frame, or $2 to $4 per square foot. The equalization of cost was made possible due to an increase in ICF contractors and skill, foreign material tariffs and mechanical costs.
Framing accounts for a significant fraction of the total cost of a project at about 17.4%. Builders can save time and money by choosing ICF over wood-framing. Wood also requires much higher maintenance and repair costs due to settling, shrinkage and subsequent finish system failures. Also staining requirements and the possibility of pest infestations from creatures like termites and woodpeckers.
Wood frame cavity wall construction continues to be notorious for mold and mildew generation, increasing costs down the road. Softwood lumber also requires more assembly items and requirements to meet various local wind-speed code requirements for the safety and security of the building. So you’ll pay more upfront and long-term. Lastly to meet current energy code requirements wood frame construction in many cases needs both internal and rigid external insulation layers.
Compared to Poured Concrete
Below-grade ICF wall systems provide substantial capital savings over conventional poured concrete or concrete block systems. Concrete block wall systems require expensive and time-consuming insulation and sealing in order for them to meet constantly advancing building codes.
We’ve seen a growth in commercial below-grade ICF foundations and grade beams to parking structures, due to easier scheduling and cost savings. Depending on the geographic location of your project, a Fox Blocks ICF foundation wall will cost you 20% less to build than either a poured concrete or concrete block basement wall.
Compared to Concrete Masonry Units (CMU)
The single most effective cost reduction is against CMU walls designed with exterior rigid insulation and weather barrier with interior furring and some form of insulation behind typical sheetrock finish. This wall assembly is very common and is the easiest for ICF to show 10-15% cost reductions and 35-50% construction schedule reductions while delivering a much higher performing wall assembly in all categories: structural, thermal, acoustic and IAQ.
Cost of ICF
Depending on the building type and execution of scope requirements, ICF may have higher up-front costs for materials. However, ICF walls installed turn-key in most cases are on par or lower than traditional wall assemblies attempting to meet the latest energy codes and, in particular, have both faster install rates and lower upfront first cost than cast in place, CMU, tilt-up and similar building methods.
Still, it will reduce the hard costs of commercial building by allowing for quick construction with minimum skilled workers and reducing transportation costs associated with other types of heavy construction.
More than anything else, these double insulated concrete walls provide many long-term cost advantages by reducing monthly utility bills, lessening maintenance costs, adding savings on repairs and rebuilding, and providing furnishings for excellent indoor environment qualities which improves any occupant’s productivity.
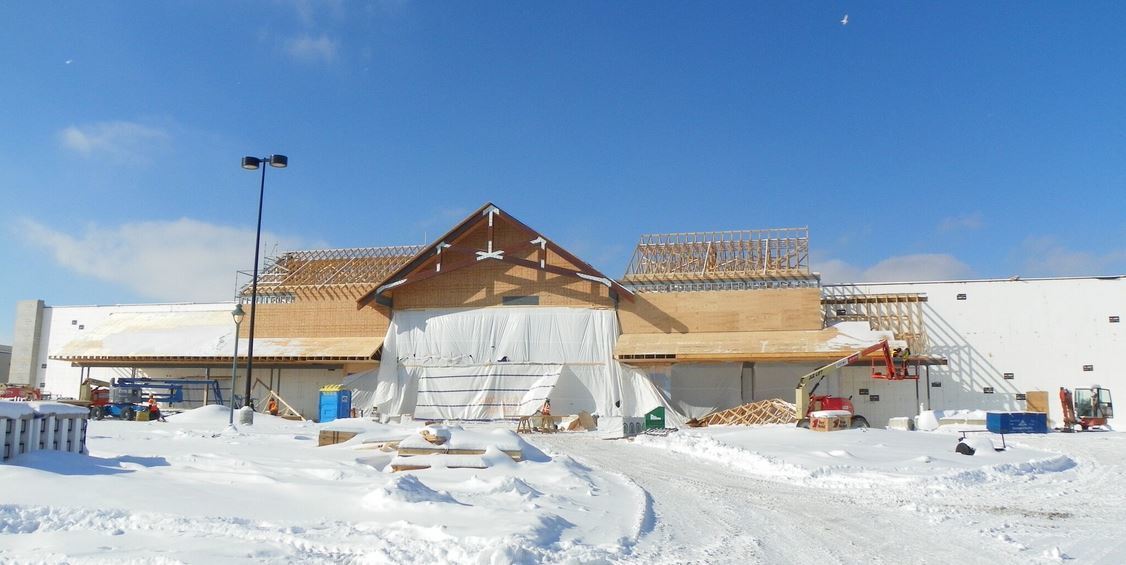
Benefits of ICF
Unparalleled Comfort and Quiet
ICF wall assembly provides indoor comfort and improves a building’s performance characteristics for the interior environment by eliminating moisture intrusion, managing the airflow and allowing for accurate climate control and mitigating sound intrusion.
Notably, the EPS Industry Alliance reports that only about one-quarter to one-eighth as much sound penetrates through an ICF wall compared to a wood-frame wall. In addition, a study out of the University of Washington reports that ICF can reduce sound transmission 200 percent better than concrete masonry unit (CMU) walls.
ICF exterior walls are a superb product for preventing noise pollution from disrupting the interior of a structure, which is a primary driver for the massive increase in devotional sector and school band halls, music halls, recording studios and megaplex theatres with THX rated sound systems choosing ICF.
Volatile organic compounds (VOC) can compromise a structure’s IAQ, which is why Fox Blocks ICFs don’t contain any. This ensures that your building is a sustainable and comfortable structure.
Durability
Fox Blocks ICFs protect a structure against mold growth, which degrades the integrity of any building. Durable products should also protect against thermal stress, which Fox Blocks ICFs does, because thermal stress can cause a building product to expand and contract, affecting a building’s long term performance.
Fox Blocks ICFs are pest-resistant and UV resistant, lowering any maintenance and protecting the interior and exterior integrity of the entire building. The strength of your building is of the utmost importance in order to achieve the highest ROI possible, and you can ensure your building will stand strong and tall with ICF.
Disaster-Resistant
Fox Block ICFs have the capability to create disaster-resistant commercial buildings that protect both the structure itself and its occupants against a plethora of natural disasters, such as hurricanes, tornadoes, floods and fires. Resilient construction is essential in new commercial construction as wildfires and severe weather ravage the world in increasing fashion due to climate change.
Fox Blocks contain steel-reinforced concrete, allowing them to resist hurricane and tornado winds exceeding 200 miles per hour, along with projectile debris traveling over 100 miles per hour. They also have a fire-resistance rating (ASTM E119) of 4 hours, allowing firefighters more time to put out fires with minimal damage.