
ICF Walls Are Less Expensive Than CMU

For building structural walls, concrete masonry units (CMU), also known as cinder or concrete masonry block (CMU), have enjoyed a significant share of the market over the last 50 years compared to other construction methods. However, the rise of insulated concrete form (ICF) technology has shown its superiority over CMUs in terms of performance, ease of installation, and ultimately cost.
ICF offers greater design flexibility, installs faster and easier, and results in a stronger and more energy efficient wall than CMU. Despite CMU’s head start in the industry, ICF continues to grow its market share.
However, there tends to be a common misconception among architects, engineers, and general contractors that CMU is less expensive than ICF. In fact, many ask us the same question: Is ICF more expensive than CMU?
You might be surprised to learn that the reverse is true. ICF construction is usually cheaper than CMU—even before factoring in the cost savings from reduced energy bills.
Cost of Materials
How can we argue that ICF costs less than CMU? The assumption has been that a typical ICF wall will cost a few dollars more than the CMU, but the cost of concrete block construction is missing an important piece of the equation: steel.
ICF is more competitive right away because it provides a reinforced monolithic concrete wall that often replaces the steel as well as the CMU.
However, the CMU contractor or block mason rarely includes any steel in their bid. The rebar, embeds, and lintel steel that are necessary for concrete block wall construction are included in a separate scope of work. Since these extra items are not part of the CMU contractor’s bid, it appears on the surface that CMU walls are more affordable. Once you consider all the necessary steel, the true cost of building a concrete block wall number is actually higher than what is typically cited.
Furring for Finishes
Check the drawings carefully for the finish system on the proposed wall assembly. For example, sheetrock can be attached directly to most ICF systems, while furring strips of some kind will be required to attach the sheetrock to the CMU. The material and labor costs of the furring strips is usually in the farmer's number and is rarely included in the CMU bid. The type of furring work, depending on complexity, can run a few additional dollars per square foot if framers are present. Even if the furring is as simple as metal channels for sheetrock– these numbers still allow CMU to bid low because the CMU contractor does not typically include furring costs in their bid.
These additional costs are often eliminated by ICFs, which if you use Fox Blocks, have built-in furring strips, 1.5” wide, at 8” on center, to streamline the installation of interior and exterior finishes. These are identified on each side of a typical ICF block by the embossed product name.
Thermal Performance
When building with CMU, insulation costs may not be included in the block masons’ bids. However, a concrete block wall alone cannot compete with the continuous double- sided insulation of an ICF system. Therefore, efforts to improve the thermal performance of CMU to approach that of ICF will drive the cost up considerably. The placement of perlite or foam inside each CMU cell may bring the wall up to code minimum, but it does not significantly improve the thermal performance of the assembly.
The average thermal performance does not mean much if the inside and outside surfaces of the wall are connected with a conductor—namely concrete. Because of this, engineers would generally recommend adding a panel of foam insulation inside with an air gap between the concrete blocks and the exterior cladding.
Should the engineer wish to replicate the ICF thermal performance, it is estimated that approximately 5+ inches of continuous foam insulation would need to be installed with the CMU wall system, which would add considerable material and labor costs.
These numbers do not take into account the financial savings for the owner after construction is complete. Due to the energy efficiency of ICF construction, owners see substantially reduced operational costs due to the decreased load on their HVAC systems.
Strength
The strength and weight of monolithic reinforced concrete, such as a fully cured insulated concrete form wall, is approximately twice that of concrete blocks.
If an architect wants a CMU wall to have strength, they may add rebar and grout in the blocks or add perimeter steel columns or pilasters to make the wall more durable and support the roof trusses. A good approximation or rule of thumb for the installed cost of steel is $3.5 per pound. Therefore, if a 10-foot column weighs 20 lbs/ft, it will cost about $700 in labor and material to install. Since these columns are not usually required for an ICF wall, the ICF wins out on structural integrity and price again.
The engineering design for an ICF follows ACI 318 for slender walls. Typically, the ICF concrete core size is smaller than the design of a CMU wall.
Speed
Many general contractors are concerned about the speed of construction and the impact on other trades. With the light-weight nature of ICFs, they can be more easily moved around the jobsite compared to concrete blocks which can be labor-intensive.
Depending on the skill and experience of your ICF crew, installation of insulated concrete forms is substantially faster than CMU. Time is money in construction, so a faster turnaround time means that contractors can more quickly move on to the next job and the owner can open their building to occupants sooner to recoup their investment.
Plus, the ICF wall assembly, as installed, is more complete with insulation and cutting strips, which can expedite the work of other trades.
Trades
Other trades, such as electricians and plumbers, may be hesitant to adopt ICF construction for fear of how their scope of work will be impacted by the seemingly new wall system. Once they understand the process, which has a minimal learning curve, they’ll quickly see that ICF is easier to work with than CMU. For example, penetrations for plumbing, HVAC, and electrical lines can be made before or after the concrete is poured by easily cutting into the EPS foam with a hot knife, electric chainsaw, or reciprocating saw.
Ultimately, when you compare all of the factors that go into building structural walls, insulated concrete forms are faster to install, more energy efficient, stronger and less expensive compared to CMU.
Why ICFs Are Replacing CMUs on Jobsites
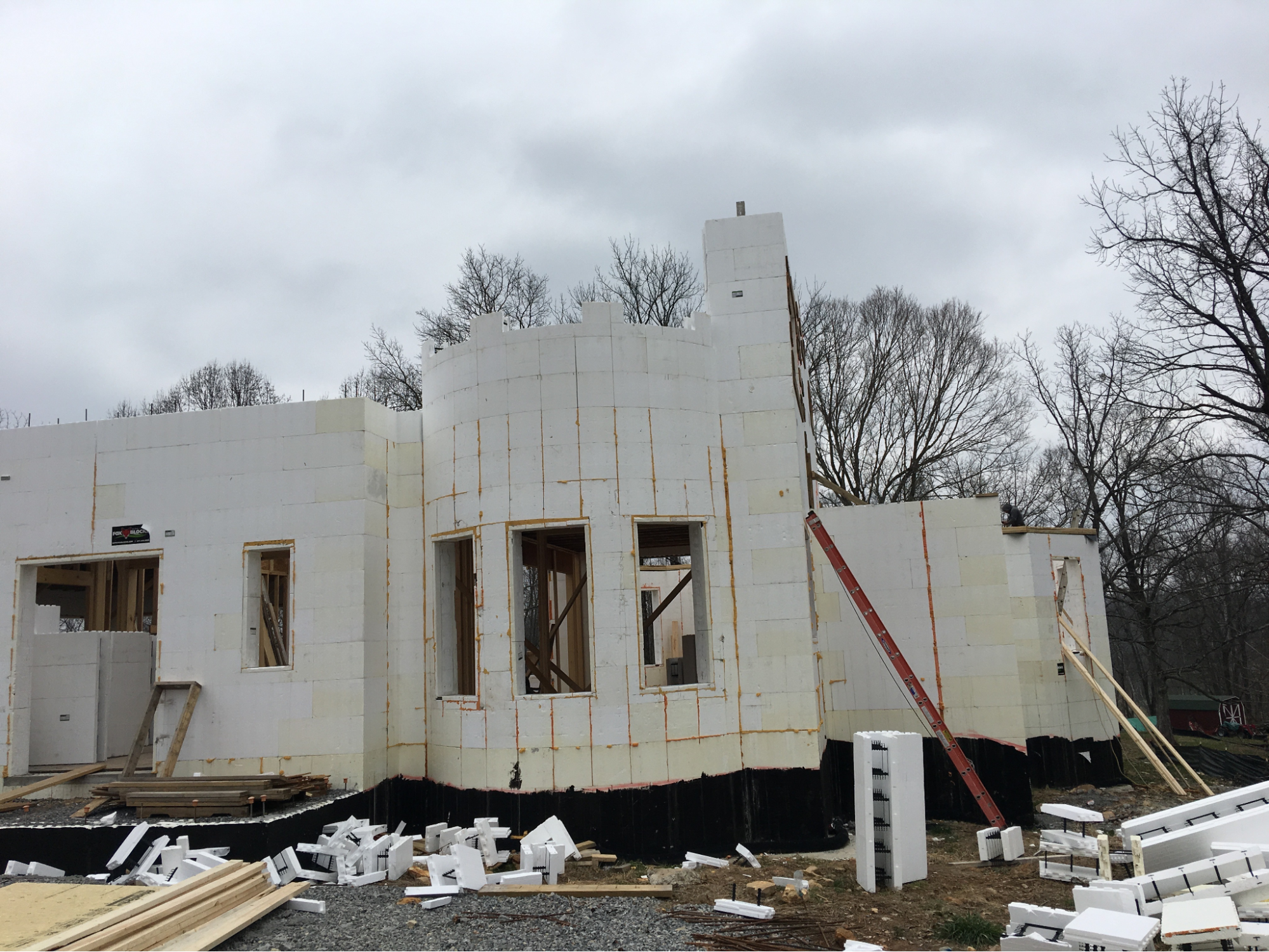
For decades, concrete masonry units (CMUs) – also known as cinder blocks or concrete blocks – have been the most common building material choice for foundation walls for homes and commercial properties. Things are improving, however. Since insulated concrete form (ICF) construction was introduced in the 1960s, they are increasingly being selected by architects and contractors for building foundations and up the wall to the roof.
There are several reasons why ICFs are replacing CMUs on jobsites. Here are the top four:
1. Durability
When you’re designing or building a home, you want it to last. When it comes to foundations and exterior walls, insulated concrete forms are one of the most durable solutions on the market.
Below grade foundation walls are the load bearing walls for the home or building. They are subjected to external pressures from the backfill and groundwater. Plus, the foundation walls must be built to be below the frost line. This means that typical basement walls are subjected to three temperature ranges – the lower third of the wall, the center third within the frost area and the top third that is above grade. The temperature changes and building science conditions influence how the wall reacts to moisture, dew points, condensation and the thermal resistance.
The weak point in a CMU foundation is the mortar, which if damaged or missing can lead to water infiltration. As a result, homeowners or property managers need to regularly inspect CMU walls for signs of deterioration. CMUs also generally have a hollow core that makes them susceptible to possible failure over time from the excessive forces, temperature changes, and moisture intrusion from either side of the wall.
ICFs with a solid reinforced concrete core and double layer of insulation address all these conditions with one product. The temperature changes are controlled by the over 5+ inches of double insulation, and the moisture, dew point and interior vapor diffusion are handled by the ICF without additional materials.
Similar attributes for ICFs work efficiently for above grade walls, the multiple benefits of an ICF wall address all the building science requirements and structural design to withstand high winds. The key is that ICFs as one building product provide all these attributes without additional materials and labor to exceed code requirements.
2. Resiliency
For an ICF, the reinforced concrete core is cushioned by the two continuous layers of thick expanded polystyrene (EPS) foam insulation on either side. As a result, ICF walls can structurally withstand tornados and hurricanes force winds up to 250 miles per hour.
In testing, it’s been demonstrated that an ICF wall can withstand flying debris and blasts with 2x4s fired from a cannon, 50-caliber machine-gun bullets, and the blast of 50 pounds of TNT from six-feet away, all with little to no damage.
ICFs are compliant to FEMA P361 and ICC 500 standards for high wind areas. Building safe rooms and storm shelters and community shelters is now commonplace using ICF reinforced concrete wall assemblies.
For resiliency, in comparison to a CMU wall with rebar, filled with grout, an ICF reinforced concrete wall is more labor, material, and cost effective.
3. Energy Efficiency
ICFs are one of the most energy efficient materials for building foundations and exterior walls. With the thermal mass of the concrete sandwiched between two layers of EPS insulation, a standard Fox Blocks ICF wall assembly has an overall assembly insulating value of R-24 with options to increase performance to levels of up to R40. Insulated concrete forms eliminate thermal bridging and are very airtight in order to eliminate drafts, regulate internal temperatures, and minimize temperature fluctuations. The building envelope helps create indoor air quality that is healthy and comfortable.
ICF basements are also comfortable spaces without drafts, mold, and mildew, that can expand the overall living space within the home.
By comparison, a CMU wall has an R-value of R-4 to R-14, which means considerable strapping, insulation, plus air/vapor barriers and sealants must be added after the CMU installation to achieve similar performance to ICFs. This requirement of materials and labor to finish the CMU walls is typically not included in the masonry quote.
4. Ease of Installation
ICF forms are lightweight modular building products that are weather-resistant, which makes them easy to store and move around a jobsite. When it’s time for installation, Fox Blocks reversible blocks stack fast and easy into place to be quickly ready for the concrete pour.
ICF systems also streamlines four key tasks required with CMU foundations and above grade walls: stripping the wall, installing continuous insulation to meet code, an air barrier, and a vapor barrier.
Completing a CMU foundation takes twice as long, or more, than an ICF wall. Once an ICF wall is completed and the roof is on the building shell, it is weather tight and ready for the interior sub-trades. This can advance the overall completion schedule by weeks and for some bigger commercial projects this has been proven to be months of time savings.
Build with the Best and Least Expensive
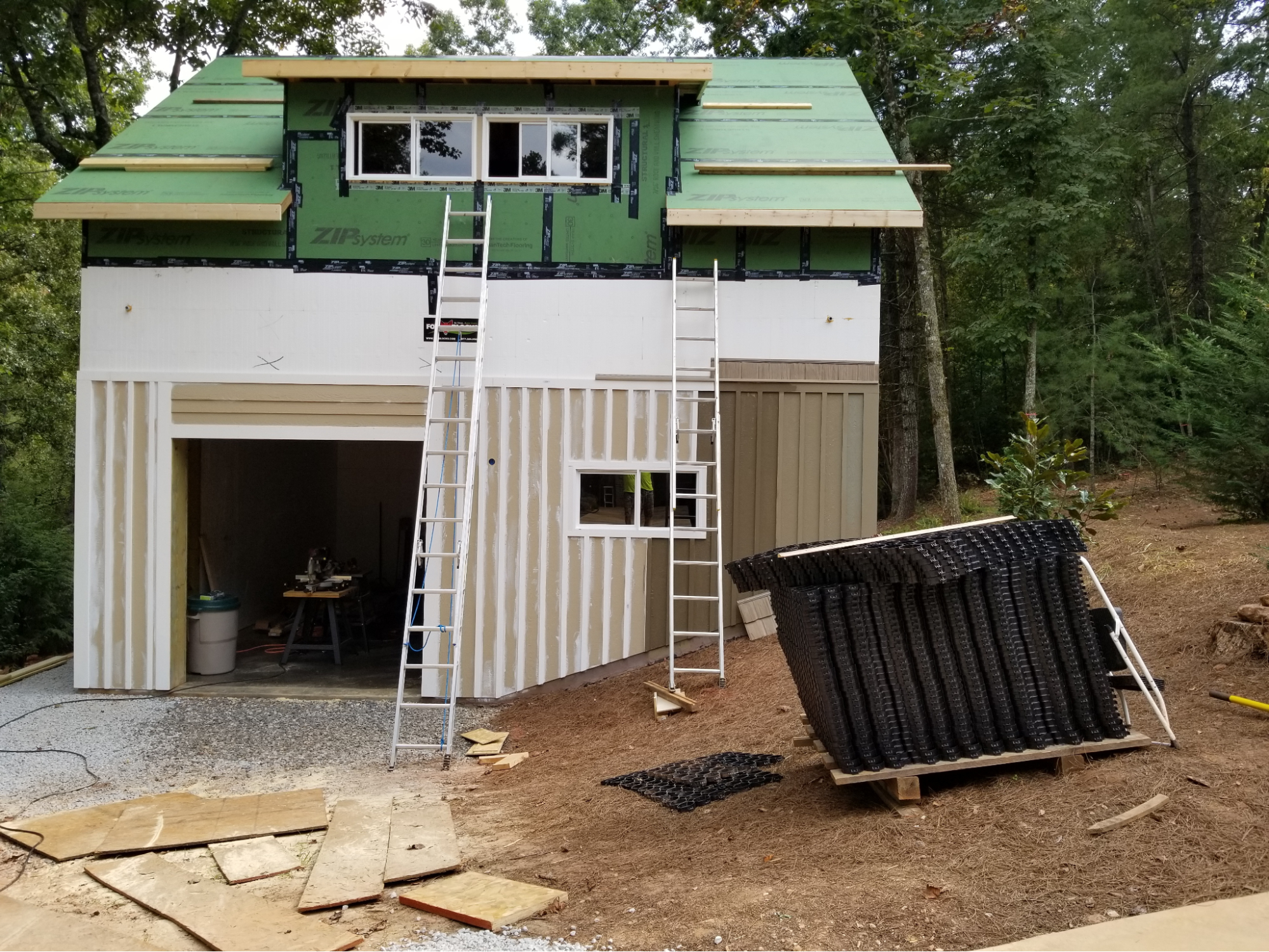
Is ICF more expensive than CMU? Absolutely not!
As everyone knows, time is money. With a chronic labor shortage in construction— residential and commercial—and an increasing material and labor costs, ICFs are an increasingly cost-effective solution that increases productivity and efficiency.
Fox Blocks ICF is the 6-in-1 solution for a wall assembly that saves time and money!
If you’re interested in learning more, contact us today!