
8 Tips for Pouring Concrete in Cold Weather and in Winter

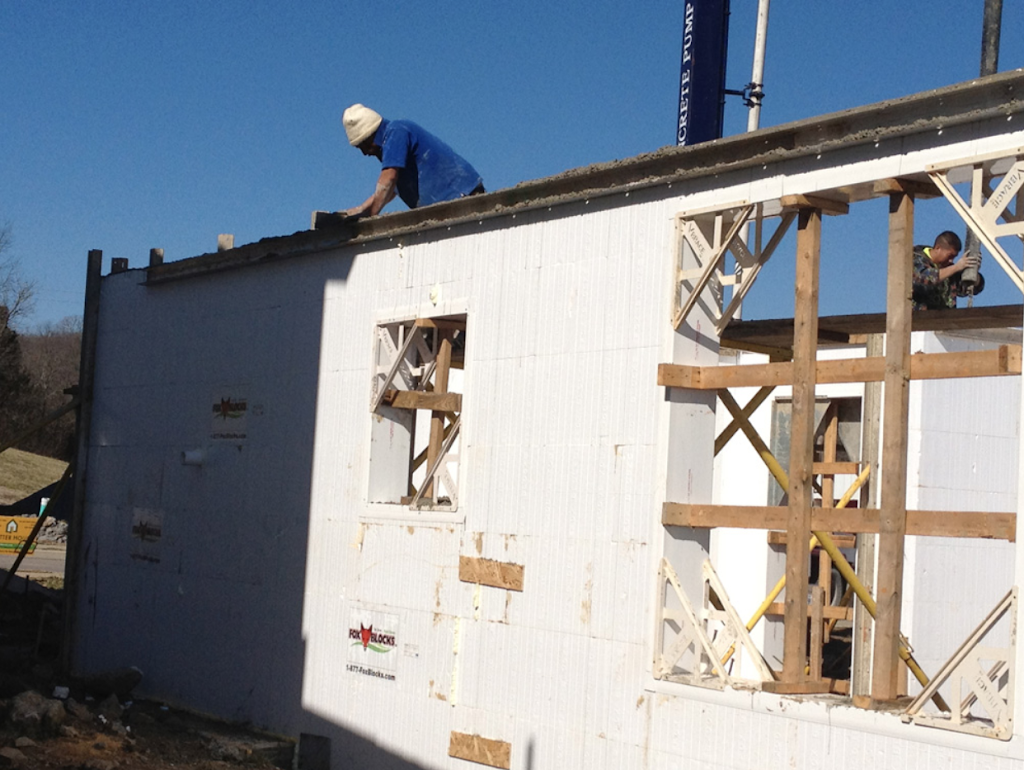
In frigid climates, cold weather concreting can increase contractors' year-round opportunities while meeting their demanding construction schedules. But,
pouring and curing concrete in cold temperatures can be challenging. For it to set correctly, you must protect fresh concrete from freezing during the first 24 hours. If it freezes, it will lose much of its strength. However, with proper safety measures and planning, you can pour concrete successfully even in cold weather conditions.
Cold Weather Concreting
In cold weather, conventional concrete placement in wood or steel concrete forms requires additional methods and procedures to prevent the concrete from freezing.
According to the American Concrete Institute (ACI), cold-weather concreting occurs when the air temperature falls below 40°F (4.5°C) for three days and below 50°F (10˚C) for more than one-half of any 24 hours during the protection period. Protection time is the time required to prevent cold weather from adversely affecting the concrete.
Of concern, freezing concrete before curing to a strength that tolerates ice expansion can reduce the concrete’s final strength by up to 50 percent. The concrete becomes weak and brittle because the water in the concrete mix freezes and expands.
Fortunately, you can successfully pour concrete in cold weather by applying several techniques that protect the concrete against freezing and ensure proper curing for a sufficient length of time. Notably, under these conditions, the concrete may develop greater strength and durability, reducing its susceptibility to thermal cracking than concrete poured at higher temperatures. Appropriate initial temperature and moisture levels will ensure standard set times and strength, even in cold weather.
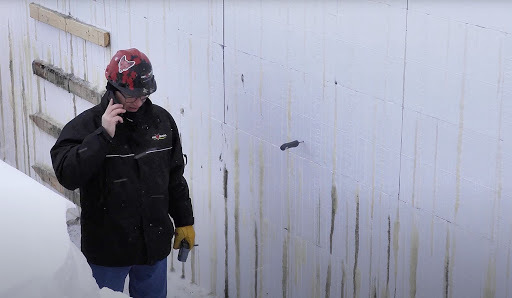
6 Tips for Pouring Concrete in Cold Weather
Before pouring concrete in cold weather, determine the concrete's special considerations and strength requirements, making sure to protect the concrete at the required temperatures until it sets. Contractors should refer to American Concrete Institute (ACI 306.1) for recommendations that identify methods for cold weather concreting.
To ensure a successful concrete pour in cold weather, consider these eight tips for code-compliant pours that result in long-lasting, strong concrete.
1. Picking the Best Concrete for Cold Weather
Vital to the success of pouring concrete in cold weather is selecting a high-quality concrete, preferably one with a minimum compressive strength of 4,000 psi or 27 Mpa. The stronger the concrete, the better for resisting the force of expanding water. Also, select air-entrained concrete that allows water to enter the tiny entrained air voids, relieving pressure from concrete capillary pores when water freezes and expands.
2. Prepare Site and Materials Before Pouring the Concrete
Before pouring concrete in cold weather, you must warm and prepare the ground and water to prevent shocking the concrete.
Redi-Mix suppliers should pre-heat water and aggregates to mix with the cement to 140˚F and 180˚F (60˚C and 82˚C) to offset the cold weather.
Remove the ice, snow, and water from the area of the pour.
Protect the workers and concrete from wind and weather that may cause quick temperature drops and swift evaporation.
Cold tools, particularly cold forms, can change the concrete's quality and strength; therefore, store your tools inside, out of the cold when not in use.
3. Carefully Monitor Temperature of Concrete
To avoid freezing that leads to slow-curing and poor-quality concrete, you must monitor the concrete temperature in cold weather.
Place concrete as soon as possible after delivery to maintain the heated mix.
Obtain a dial pocket thermometer or an infrared thermometer to continually test the concrete temperature, careful to ensure it stays above the required 50°F (10˚C) for the concrete to keep gaining strength — and make sure it does not drop below 40°F (4.5°C) in 24 hours. Keeping a well-defined chart on the air and concrete temperature will help you quickly address any unexpected temperature changes.
Heat enclosures used to maintain concrete temperature during hydration and curing must be wind- and water-proof.
Be ready with blankets, lights, and supplement heating if the sun sets just as you're ready to start finishing.
Ensure the safety of enclosures and heating systems from fire and fumes.
4. Accelerating Admixtures Increase Set Times for Concrete
Set times for poured concrete significantly increase in cold weather. However, once concrete achieves a compressive strength of 500 PSI or 3.5 Mpa, cold weather causes little damage to the fresh concrete. Therefore, the sooner you attain the compressive strength, the less likely the pour will fail.
Adding accelerants to concrete immediately before or during mixing concrete increases the hydration rate, shortens the setting time, speeds up curing, and increases the early strength development rate. However, if using steel-reinforcements, avoid additives with rust-causing calcium chloride since it can crack the concrete.
5. Adding More Cement Increases Hydration
Adding 100 pounds per cubic yard more of cement to the mixture will provide extra heat, quicken hydration, and minimize water forced to the concrete's surface (bleeding).
Increasing the cement to water ratio (lowering slump) raises the cement paste density, thus adding weather-resistant qualities and concrete strength.
6. Worker Safety When Pouring Concrete in Cold Weather
In frigid weather, employee safety protects the worker, contractor, and the project's success. OSHA's cold stress guidelines provide a good start for creating a safe working environment. Teaching employees to recognize the early signs of cold stress and frostbites can prevent serious, long-term problems.
ICFs: A Better Solution to Pouring Concrete in Cold Winter
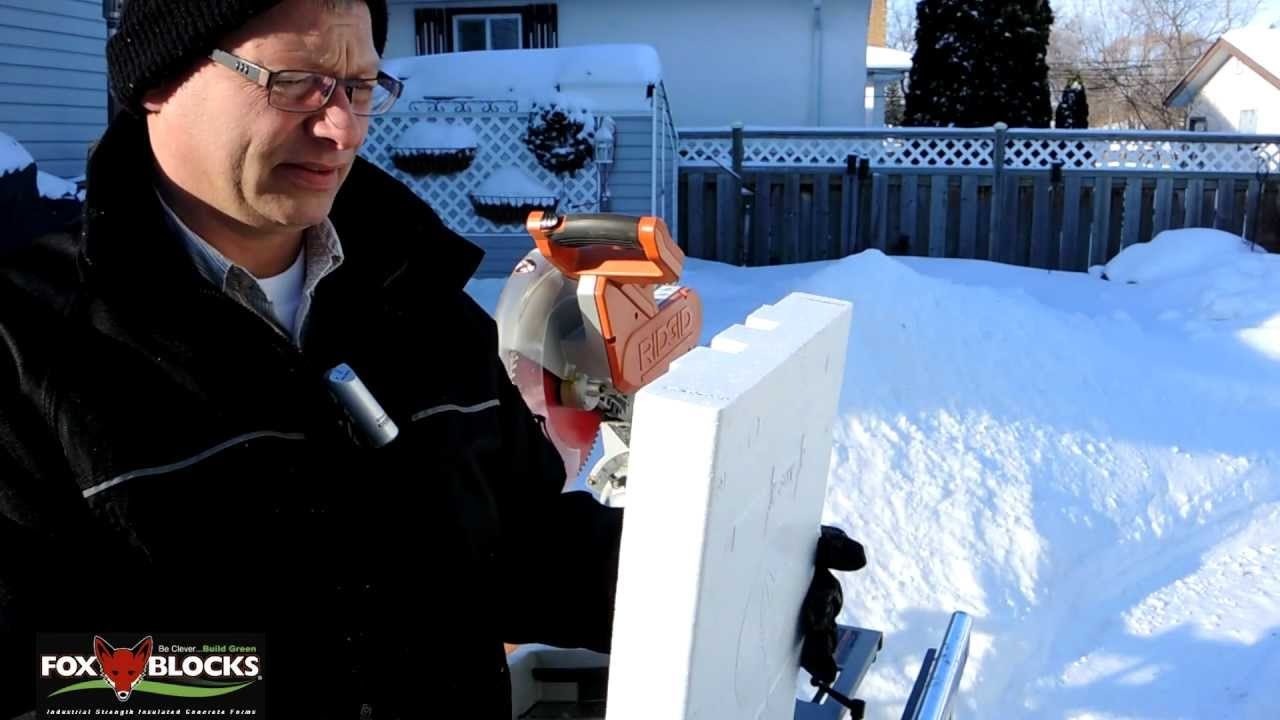
Cold-Resistant and Fast FOX Block ICF Construction
Fox Block insulated concrete forms (ICFs) allow contractors to successfully pour concrete during the cold winter months without the problems associated with traditional concrete pours.
The insulated forms' high continuous insulating qualities allow pouring concrete into below- and above-grade ICFs with ambient temperatures as low as -5° F (-15°C), with the top of the form protected with insulating blankets. The insulated forms shield the concrete from freezing or rapid drying, allowing completions of the curing process. ICF construction can significantly lengthen your construction season, potentially allowing you to pour year-round, hastening completions, and reducing weather-related delays.
The double layers of insulation retain the heat generated by the hydration of the concrete. This heat remains in the concrete core of the ICF wall, enhancing the overall concrete strength.
The site or wall assembly does not require additional hoarding or heating, just insulating the wall's top or any exposed edge. Using the Fox Buck provides insulating protection around wall openings.
Moreover, Fox Block Series, all in one wall system, blends five-building steps into one, including insulation, structure, air barrier, vapor retarder, and attachment — quickening project delivery time by eliminating the need to coordinate various trades.
Case Studies Show ICF Protects Concrete from Freezing
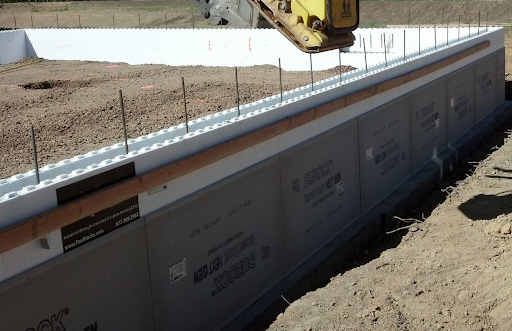
Carleton College in Northfield, MN, constructed a three-story ICF dormitory in the brutally cold winter. After pouring the concrete into the forms, the crew pushed a thermometer through the foam into the freshly-poured concrete core. While the jobsite temperatures stayed around 19°F, the thermometer embedded in the concrete remained near 100 degrees for a full 24 hours.
A case study in Fairbank, AK started with hot water, so the concrete was 95°F coming out of the truck. The crew then taped R-11 fiberglass batt insulation on the top of the forms and over the window and door bucks. After seven days of -10°F jobsite temperatures, the form’s inside temperatures never dropped below 80-85°F.
Further Benefits of Fox Block ICFs in Cold Climates
High-Performing, Energy-Efficient ICFs
Fox Block ICF offers numerous benefits for colder climates, other than allowing for concrete pours in freezing temperatures. Fox Block ICFs with R-values above 23 create comfortable and warm buildings and homes, lessening mechanical heating use by 60 percent. The high thermal mass ICF walls also reduce energy consumption during the winter by absorbing heat energy from sun-facing windows, along with the heat produced from lighting, cooking, and appliance use. The absorbed heat slowly releases in the night as temperatures drop, keeping a building or home warm and lessening the need for mechanical heating.
Moisture-Resistant, Durable ICFs
Frigid weather can diminish a building’s durability, especially with a wood-framed structure. During cold weather, air leaks outward through wood-framed walls, ultimately colliding with the back of the cold shealthy, changing the air's moisture into frost. Of concern, warming spring temperatures melt the frost, creating rot, damaging ceilings and walls, and degrading the building's integrity. Fortunately, durable, airtight, and moisture-resistant ICF walls stop condensation year-round, including the winter months; therefore, they resist unhealthy and structurally damaging mold.
Utilizing Fox Blocks simplifies cold weather construction, extending the construction season and providing all the natural characteristics of a Fox block wall assembly.
For further questions on pouring concrete in winter, please connect with a Fox Blocks professional.