
How to Speed Up New Home Construction

In these times of construction labor shortages and escalating lumber prices, insulated concrete form (ICF) wall systems can help builders increase home construction and stay on budget. Lightweight and sturdy ICFs, like Fox Blocks, speed up new home construction with quick and easy installation, guaranteed availability, and both hot and cold temperature resistance.
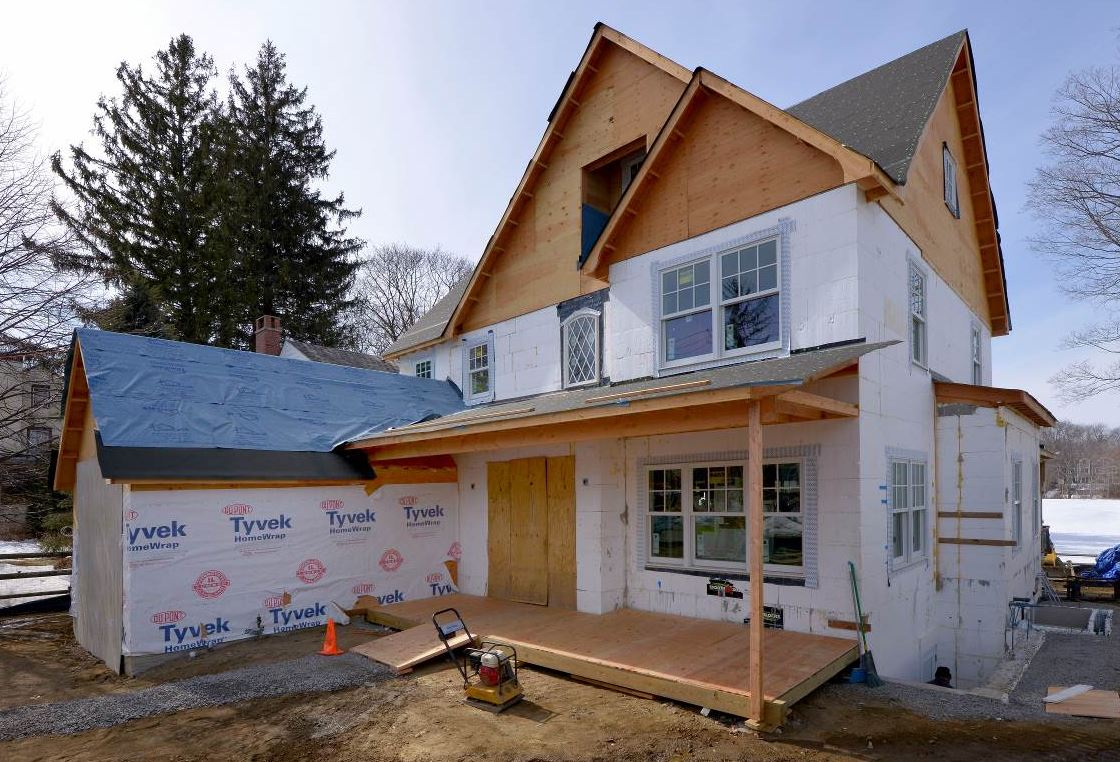
Labor and Lumber Shortages Slow Home Construction
Residential construction has bounced back to pre-recession levels, with housing starts at a near 10-year high of 1,496,0001,496,000. However, many builders still struggle to stay on schedule and turn a profit due to labor shortages and rising lumber costs.
The NAHB/Wells Fargo Housing Market Index (HMI) - Table 1, reports that in 2020, 85 percent of builders in the U.S. expect serious challenges in scheduling and budgeting due to labor cost and availability. Similarly, 66 percent of builders expect problems due to the rising cost of materials, especially lumber. These challenges threaten to slow the momentum in home construction despite housing shortages and historically low-interest rates.
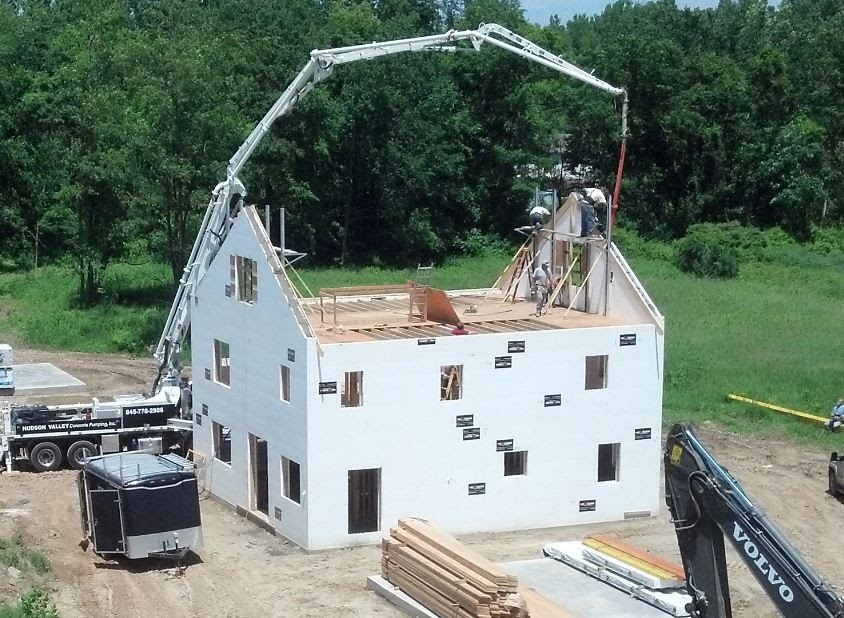
Construction Labor Shortages
Two main factors contribute to construction labor shortages in the U.S.: the industry not attracting millennials and the current immigration policies for undocumented immigrants. Labor shortages on construction projects can lead to scheduling delays, higher wages and home prices, reduced profits, and even canceled sales.
The Rising Cost of Lumber
After COVID-19, lumber prices rose because the mills shut down in April and May 2020, anticipating a slowdown in demand for lumber; however, the opposite happened. After an initial drop off, the housing market quickly recovered in mid-April.
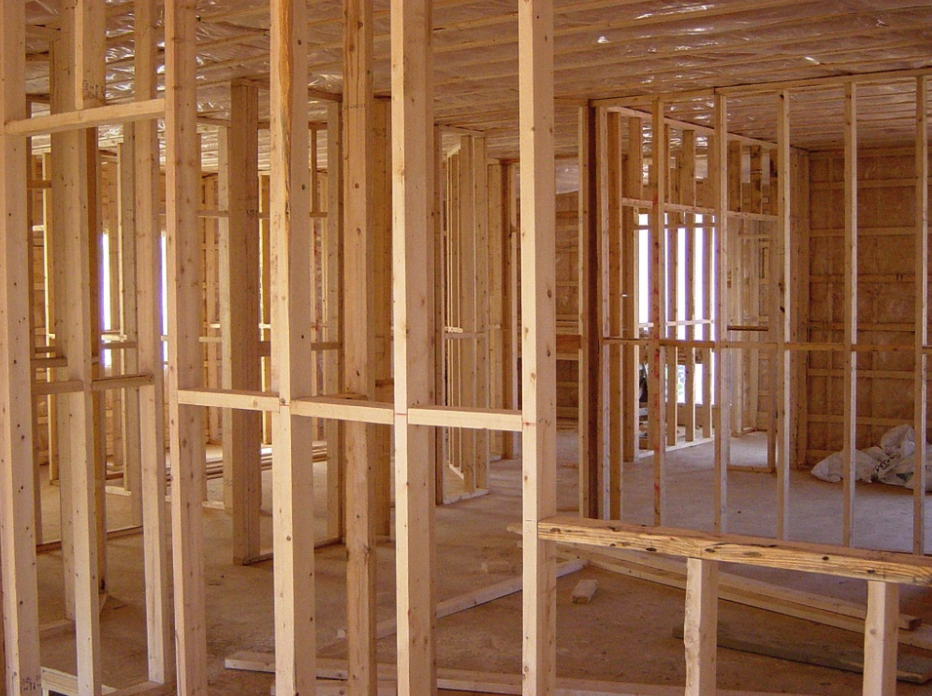
Since then, prices have nearly doubled from pre-pandemic prices of $425 to $830 per thousand board feet, due to a shortage of lumber. The Trump administration's tariffs on Canadian lumber (averaging more than 20 percent) continue to elevate lumber prices. The expense (and lack of lumber availability) threaten to slow project delivery time and cut into profits.
8 Ways ICF Helps Contractors Expedite Home Construction and Stay on Budget
- Sturdy, yet lightweight ICFs allow installers to get the work done much faster and easier than wood-frame construction. ICF construction involves a small group of trained workers laying the forms for a single-story house in one day. The next day they pour the concrete. In just two days, ICF builders can frame and wrap a house, making it ready for the roof and the inside and outside finishings.
- ICF construction reduces labor requirements and eliminates the need to coordinate multiple trades because ICF combines 6-building steps into one: the structure, continuous insulation, air barrier, weather-resistive barrier, vapor retarder, and attachment.
- The simplicity of ICF construction requires a short learning curve for both the builder and his or her workers.
- ICF construction saves time because it eliminates the need for caulking or sealing as well as interior and exterior barriers.
- After pouring the concrete into the forms, subcontractors can easily and quickly install HVAC, plumbing, and electrical, because of the ease in cutting the foam.
- ICF walls' strength and durability protect a home from storms, vandalism, fires, and site accidents during the building process, helping the builder complete the project on time. A tornado, fire, or human error can set a wood-frame construction project back for weeks.
- Builders can steer clear of construction delays due to lumber shortages and circumvent volatile lumber costs by choosing readily available and price-stable ICF.
- Builders won’t get behind due to extreme heat or cold, because temperature-resistant ICF's allow for year-round construction.
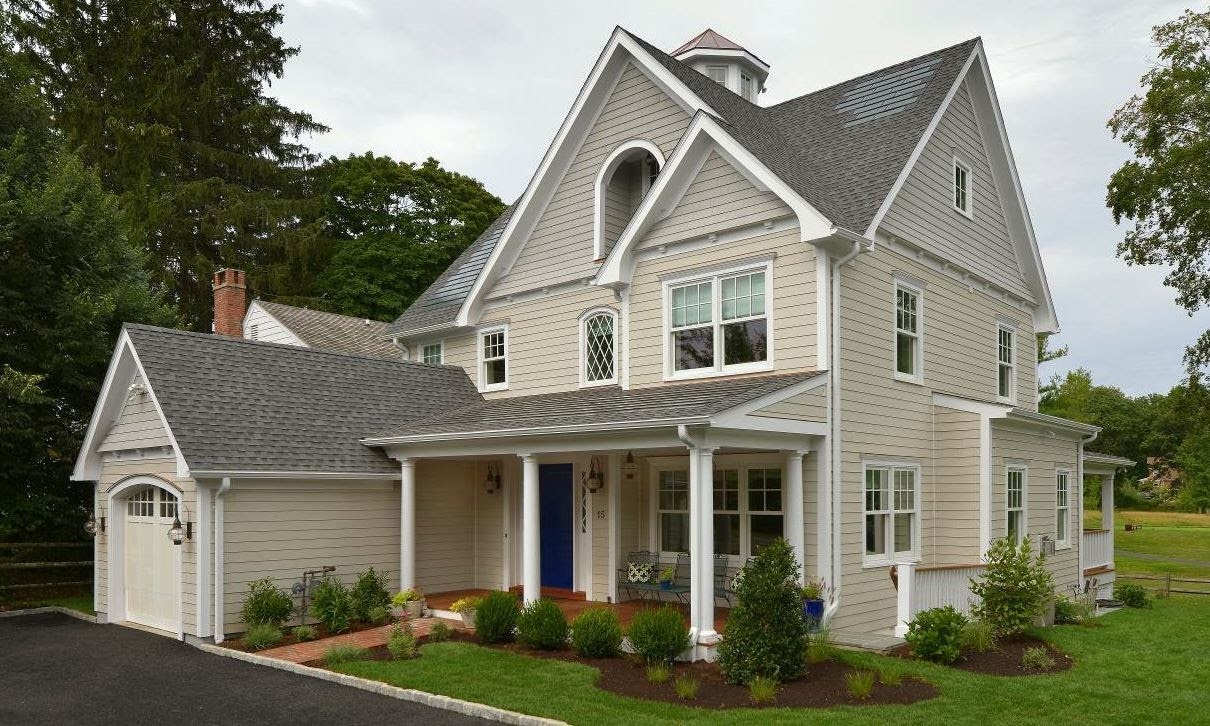
ICF Home Construction Has Many Benefits
Fox Blocks ICFs have much more to offer builders and homeowners than reduced construction time:
- Energy-efficient ICFs exceed ASHRAE/ANSI 90.1 energy code requirements, with a high thermal mass and an R-value of 23.
- Disaster-resistant, they can withstand winds of over 200 mph and debris flying over 100 mph.
- A perm rating of less than 1.0 stops the accumulation of moisture in the walls, which can lead to mold growth that is unhealthy and can degrade the integrity of the home.
- ICFs create homes with good acoustics. Fox Blocks have a Sound Transmission Classification (ASTM E90) of 4-inch=STC 46, 6- and 8-inch = STC 50+.
- They create healthy homes because of the air-tightness, and they contain little to no VOCs.
- Fox Blocks ICFs have a fire-resistance rating (ASTM E119) of 4 hours for the 6-inch blocks and 2 hours for the 4-inch blocks.
- ICFs produce durable homes because they lack organic materials, making them less susceptible to termite damage. However, for waterproofing and termite protection, Fox Blocks suggests Polyguard Products, Inc. 650 XTM, or 650 XTP membranes.
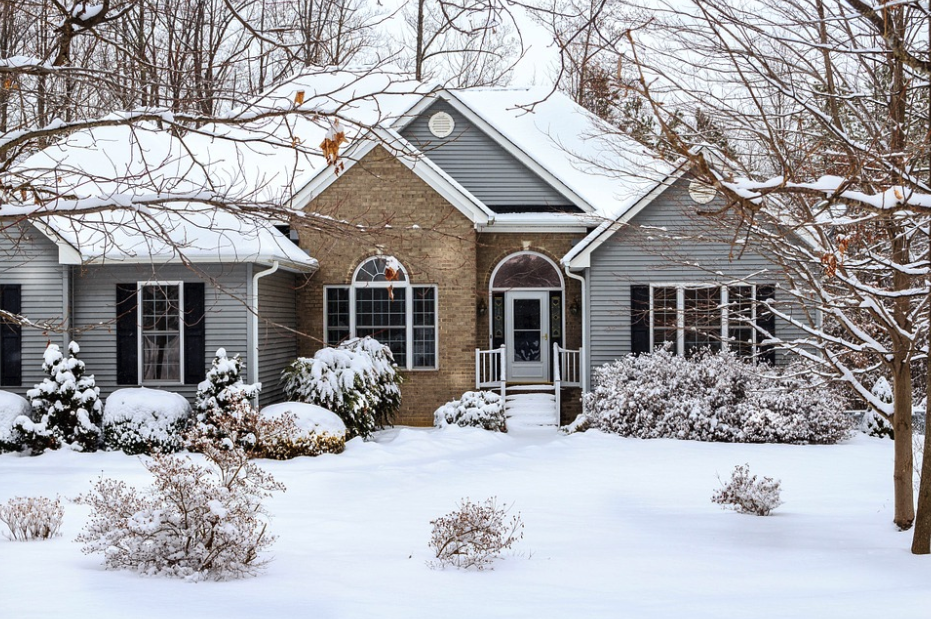
Fox Block ICFs help builders expedite home construction by combating labor and lumber shortages - which can destroy a project's timeline and budget. Lightweight, durable, and temperature-resistant ICFs install easily and quickly allow both the builder and subcontractors to complete their jobs on time and on budget.
Notably, Fox Blocks ICFs offer a viable option for energy-efficient, healthy, and moisture and disaster-resistant below-grade walls and high-performing above-grade walls for single and multi-story buildings.
Please contact Fox Blocks professionals for more information on how to expedite new home construction with Fox Block ICFs.