
The New Basement: A Modern Housing Innovation

At a time when affordable housing is a prime concern, the one design element that is revolutionizing homes is a usable, comfortable, livable basement. No longer are basements a scary, damp, and musty area under your home.
Early basements did include insulation and materials to stop mold or mildew, but it wasn’t until the 1950’s that concrete floors in basements were seen in new homes. Basements were always considered storage space and an area for the utilities—the furnace, boiler, hot water tank, sump pump, and maybe a laundry room and workshop.
Because the space was not used often, early basements did not consider the unhealthy environment without insulation or materials to mitigate mold and mildew. In fact, some basements of older homes still had dirt floors, and most homes with an unfinished basement did not add resale value to the home in any way.
Climate Zone
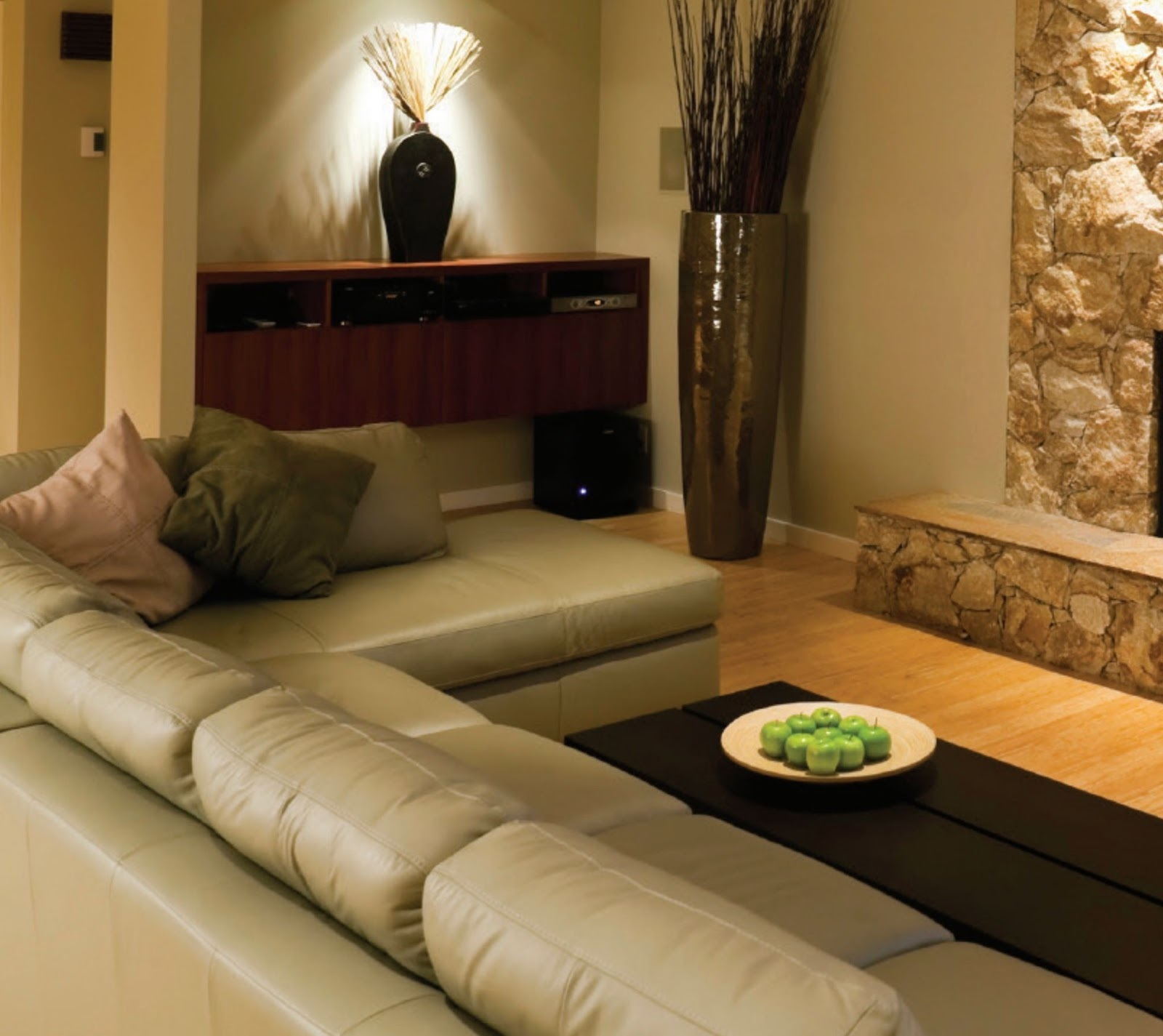
Geography has a lot to do with the below grade design. In the northern climate zones that experience freezing temperatures, frost is the big concern. If not addressed, frost can create movement under a foundation. Footings and below grade walls must be built to be below the designated frost line, which is typically 4’ below finished grade.
This meant that there could be possibly 6’ plus under the finished floor level, so it evolved into making it a usable space with a 7’ or 8’ ceiling height in order to create a usable below grade basement space in the home. As the climate zones change, moving south, the frost line is not as deep, and it moves up to 2’ or even zero. This leads to crawl spaces in most southern areas or slab on grade with no basement.
However, as basements became the norm for new home construction in the northern climate zones many building science issues had to be developed to make the space more usable. Issues to be addressed were water intrusion, condensation (dew point), thermal transfer, and concrete block deterioration from moisture and frost.
All of these issues created musty smells, mildew, and a generally cold, unhealthy atmosphere. The attempt to add insulation, moisture control, and finishes led to studies that found a majority (>90%) of finished basements contained toxigenic molds that impacted the whole home as well as the overall health and energy efficiency of the building.
Building Codes
Building code changes over the years started to address below grade walls with insulation requirements, and a vapor retardant to generally rectify the mold issue. As the codes improved toward more energy efficiency below grade walls there was more building science scrutiny on the assemblies to alleviate the health issues related to mold.
The finishing of the below grade walls had to address moisture intrusion and condensation. Studies showed that materials that retain moisture such as regular wood studs and fiberglass insulation may be an issue in finishing these walls. The problem was condensation appearing on the inside face of the poly vapor barrier and saturating the fiberglass insulation, which developed mold, plus a high moisture content in the wood strapping that caused it to rot. The application and sequencing of the wall assembly materials was, and still is, evolving.
Below grade walls required pressure treated strapping to prevent rotting, and insulation was expanded to be full height continuous insulation, so the material changed to either rigid or non-absorbent rock wool type or XPS with a sealed poly vapor barrier. This design addresses condensation and any moisture absorption to eliminate the chance of mold development.
Drainage and Waterproofing
The other below grade issue was the methodology and quality of the exterior drainage system and waterproofing system applied to the below grade walls. The three main goals for managing water below grade are to:
1. Reduce water in the soil with perimeter drainage systems
2. Stop water vapor from soil with vapor barrier, and
3. Stop condensation with thermal control.
More attention was paid to the control of rainwater, ground water, and drainage away from the exterior walls. The installation of a perimeter below grade drainage system for all soil types became a mandatory application. Control of exterior drainage down the wall face and away from the building was a key element that would prevent water and moisture from getting behind exterior finishes and below grade waterproofing.
Best Option for Below Grade Walls
The newest methodology is for the use of double layers of rigid insulation directly applied to the foundation wall behind and between the 2x wood strapping. This is to achieve the continuous R-Value to meet the minimum code requirements and control moisture levels in the wood studs.
In a review and comparison of labor and materials to meet code, one system was deemed to be the ultimate solution and meet all these requirements for below grade walls – insulated concrete forms (ICF).
Benefits of Insulated Concrete Forms As a Wall Foundation
An ICF foundation wall provides a 6-in-1 building product solution, one with a structurally superior thermal resistance that exceeds code minimums and has built-in vapor barrier and air barrier systems and fastening strips for attachment of finishes— not to mention, a compatibility with EPS waterproofing applications.
Most ICF residential foundation walls may be designed with a 6” or 8” reinforced concrete core size. The double layer of continuous insulation, one layer of the exterior face and one layer on the interior face provide an R-Value of R23, which exceeds energy codes. The concrete provides a vapor and air barrier. The dew point of this wall assembly occurs within the concrete, which results in no condensation anywhere near the interior face of the wall. ICFs do not promote mold or mildew and they do provide a healthy wall assembly.
Along with all the other benefits of ICFs, the speed of construction is the most impressive. The modular blocks, typically 16”x48” are placed quickly, rebar is installed, and the full height of the wall is filled with concrete. The reinforced concrete walls, without any additional materials, are then ready for exterior waterproofing and interior finishes. There are several types of waterproofing systems—liquid or membrane, that may be installed over ICF. These products must be compatible with the EPS insulation, and some may require a primer ( Always check with the ICF manufacturer).
New Basement
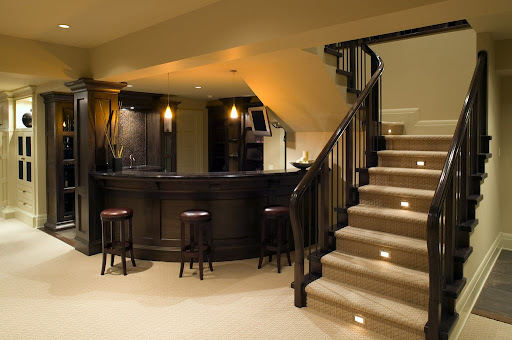
The evolution of the basement has now created a modern space and the realization that it is an extension of the liveable area. The benefits of having a well-insulated and healthy space is that the design can include bedrooms, family rooms, media rooms, and granny suites.
Basements are now appreciated as a modern convenience. This large area under the main floor can now be modernized with beautiful finishes and can, in fact, become an extension of the overall usable living space. The square footage under the house’s main floor can be attractive and comfortable and add value to the property.
ICF materials provide an excellent option for not only below grade walls for finished basements, but also for above grade walls.
If you’re interested in learning more about ICF, contact Fox Blocks for more information!